Method for efficiently preparing nickel-coating copper composite powder through ultrasonic chemistry
A technology of nickel-coated copper and composite powder, which is applied in liquid chemical plating, coating, metal material coating technology, etc., can solve the problems of many chemical reagents, high cost, and difficult industrial production, and achieve a nickel-copper bonding interface The effects of purity, improved reaction efficiency, and accelerated reaction rate
- Summary
- Abstract
- Description
- Claims
- Application Information
AI Technical Summary
Problems solved by technology
Method used
Examples
example 1
[0018] Example 1: Prepare 327g of nickel-coated copper powder.
[0019] 1) According to the ratio of the amount of substances of 1:1, weigh 372g of complexing agent ethylenediaminetetraacetic acid disodium salt (EDTA-2Na) and 129.6g of nickel chloride respectively; , mix the two and stir evenly;
[0020] 2) Slowly add concentrated ammonia water with a concentration of 34% by volume, adjust the pH value of the solution to 9.0, set the volume to 3L, raise the temperature of the mixed solution to 95°C, and keep it warm for 300s;
[0021] 3) Start to apply high-energy ultrasonic vibration treatment to the nickel salt mixed solution, the ultrasonic power is 1000W, the frequency is 50MHz, and the ultrasonic oscillation time is 20 minutes;
[0022] 4) With ultrasonic treatment, uniformly add 300 g of copper powder with a particle size of 45 μm, stir evenly, and then adjust the pH value of the solution to 14 with 3 mol / L KOH;
[0023] 5) Slowly add 210ml of anhydrous hydrazine N wit...
example 2
[0025] Example 2: Prepare 654g of nickel-clad copper powder.
[0026] 1) According to the ratio of the amount of substances 1:1, weigh 744g of complexing agent ethylenediaminetetraacetic acid disodium salt (EDTA-2Na) and 259.2g of nickel chloride respectively; , mix the two and stir evenly;
[0027] 2) Slowly add concentrated ammonia water with a concentration of 34% by volume, adjust the pH value of the solution to 10, set the volume to 6L, raise the temperature of the mixed solution to 95°C, and keep it warm for 300s;
[0028] 3) Start to apply high-energy ultrasonic vibration treatment to the nickel salt mixed solution, the ultrasonic power is 2000W, the frequency is 50MHz, and the ultrasonic oscillation time is 10 minutes;
[0029] 4) With ultrasonic treatment, uniformly add 600 g of copper powder with a particle size of 45 μm, stir evenly, and then adjust the pH value of the solution to 14 with 3 mol / L KOH;
[0030] 5) Slowly add 420ml of anhydrous hydrazine N with a co...
PUM
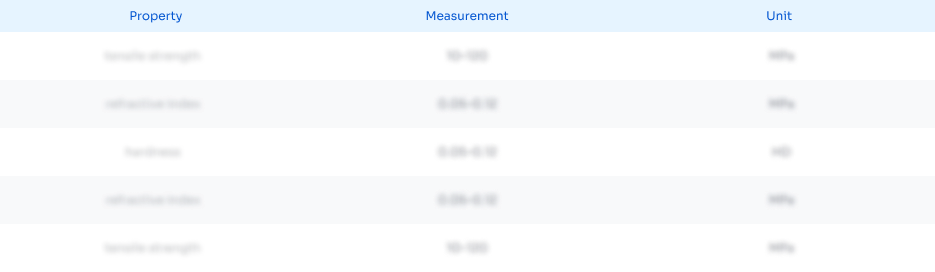
Abstract
Description
Claims
Application Information

- R&D
- Intellectual Property
- Life Sciences
- Materials
- Tech Scout
- Unparalleled Data Quality
- Higher Quality Content
- 60% Fewer Hallucinations
Browse by: Latest US Patents, China's latest patents, Technical Efficacy Thesaurus, Application Domain, Technology Topic, Popular Technical Reports.
© 2025 PatSnap. All rights reserved.Legal|Privacy policy|Modern Slavery Act Transparency Statement|Sitemap|About US| Contact US: help@patsnap.com