Preparation and construction method of epoxy grouting material for track filling and secondary grouting
A technology of epoxy grouting and secondary grouting, which is applied in the direction of track, track maintenance, track laying, etc. It can solve the problems of poor product toughness, low strength, large expansion rate, etc., and achieve low non-expansion shrinkage rate and high bonding strength , the effect of dense pores and less
- Summary
- Abstract
- Description
- Claims
- Application Information
AI Technical Summary
Problems solved by technology
Method used
Image
Examples
preparation example Construction
[0065] The preparation method of the high-strength precision non-shrinkage epoxy grout of the present invention:
[0066] Preparation of component A: Accurately weigh the above-mentioned glycidyl ether reactive diluent, toughening agent, leveling agent, defoamer, antioxidant and silane coupling agent or titanate coupling agent at 15-60°C , placed in a stirred tank at 300 rpm for pre-mixing for 20 minutes. Then weigh the above-mentioned bisphenol A type epoxy resin and add it into the pre-mixed stirring tank, and keep the temperature constant for blending for 1 hour. Finally, the material is packaged according to specific gravity as component A.
[0067] Preparation of component B: It is prepared by reacting polyetheramine and 2,4,6-tris(dimethylaminomethyl)phenol at a ratio of 2:1 at 60-80°C and placed under stirring at 15-60°C Re-disperse in the kettle for 30min. Packing according to specific gravity discharge as B component.
[0068] Preparation of component C: Take sand...
test approach 1
[0072] Table 3 Test scheme 1 mass ratio
[0073]
[0074] Take the prepared A, B, and C three-component materials and mix them at a mass ratio of 80:24:400. According to the test standard in Table 3, the following performance tests are carried out, and the test results are shown in Table 7
[0075] ①. Test the flow value of the blend.
[0076] Carry out in accordance with GB / T50448-2008 regulations. Dimensions of conical circular die: height 60±0.5mm, inner diameter of upper mouth 70mm±0.5mm, inner diameter of lower mouth 100mm±0.5mm, outer diameter of lower mouth 120mm. Test plate: flat glass with an area larger than 300mm*300mm.
[0077] ②, linear shrinkage
[0078] The test is carried out in accordance with the regulations of HG / T2625-94, which is suitable for the linear shrinkage of the material from the gel state after mixing.
[0079] ③, flexural strength, compressive strength
[0080] The test of compressive strength and flexural strength shall be carried out a...
test approach 2
[0088] Table 4 Test scheme 2 mass ratio
[0089]
[0090] Take the A, B, and C three-component materials prepared in Test Scheme 2 and mix them at a mass ratio of 80:32:400. Test according to the corresponding method in Test 1, and the test results are shown in Table 7.
[0091] Experiment 3
PUM
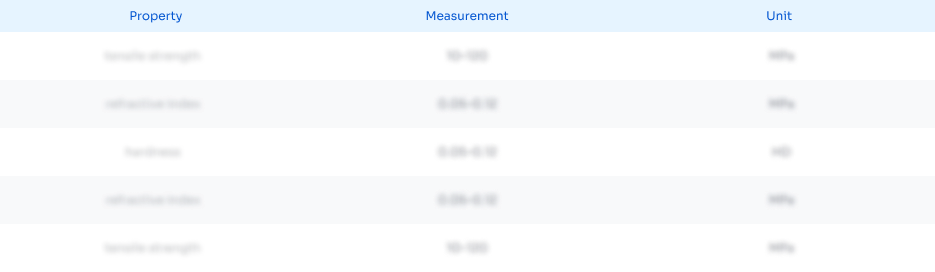
Abstract
Description
Claims
Application Information

- Generate Ideas
- Intellectual Property
- Life Sciences
- Materials
- Tech Scout
- Unparalleled Data Quality
- Higher Quality Content
- 60% Fewer Hallucinations
Browse by: Latest US Patents, China's latest patents, Technical Efficacy Thesaurus, Application Domain, Technology Topic, Popular Technical Reports.
© 2025 PatSnap. All rights reserved.Legal|Privacy policy|Modern Slavery Act Transparency Statement|Sitemap|About US| Contact US: help@patsnap.com