Method for prolonging service life of face milling cutter based on heat pipe phase changes
An end mill and heat pipe technology, applied in the field of mechanical processing, can solve problems such as patents that have not yet been seen, and achieve the effects of reducing manufacturing costs, cutting temperatures, and low prices
- Summary
- Abstract
- Description
- Claims
- Application Information
AI Technical Summary
Problems solved by technology
Method used
Image
Examples
Embodiment 1
[0041] Such as Figure 2a-Figure 2c As shown, the schematic diagram of the temperature change of the end mill cutting edge with time under different conditions of use, where: the specification of the end mill used in the experimental measurement is Side cutting amount a c Take 14mm.
[0042] Figure 2a Indicates: when no cutting fluid and heat pipe 1 are used, the schematic diagram of the change of the machining temperature of the cutting edge of the end mill with time; Figure 2b Indicates: when cutting fluid is used, the schematic diagram of the temperature change of the cutting edge of the end mill with time; Figure 2c Indicates: when heat pipe 1 is used, the schematic diagram of the change of machining temperature of end mill cutting edge with time.
[0043] The measurement results show that: under the same processing conditions, the cutting temperature of the end mill using the heat pipe 1 is lower than that of the cutting fluid.
[0044] Since the three-sided edge ...
Embodiment 2
[0047] Such as Figure 3a-Figure 3c As shown, the wear condition of the outer tip of the main cutting edge measured by the end mill after processing several grooves under different conditions of use, where: the specification of the end mill used in the experimental measurement is Side cutting amount a c Take 28mm; Figure 3a Indicates: when cutting fluid and heat pipe 1 are not used, the wear condition of the outer tip of the main cutting edge measured by the end mill after machining 1490 grooves; Figure 3b Indicates: when cutting fluid is used, the wear condition of the outer tip of the main cutting edge measured by the end mill after machining 1751 grooves; Figure 3c Indicates: When heat pipe 1 is used, the wear condition of the outer tip of the main cutting edge is measured after the end mill has processed 2000 grooves.
[0048] The measurement results show that under the same processing conditions, the flank wear of the end mill using heat pipe 1 is lighter than that...
Embodiment 3
[0051] Such as Figure 4 As shown, the schematic diagram of the service life of the end mill under different conditions of use, where: the specification of the end mill used in the experimental measurement is Side cutting amount a c Take 50mm; SD means: without using cutting fluid and heat pipe 1; CF means: using cutting fluid; HF means: using heat pipe 1. The subscripts 1 and 2 respectively indicate the number of end mills under different cooling conditions.
[0052] The measurement results show that: under the same processing conditions, the life of the end mill using the heat pipe 1 is longer than that of the end mill using cutting fluid.
[0053] In addition, the cutting fluid used in this experiment is the cutting oil commonly used in the manufacturing industry.
PUM
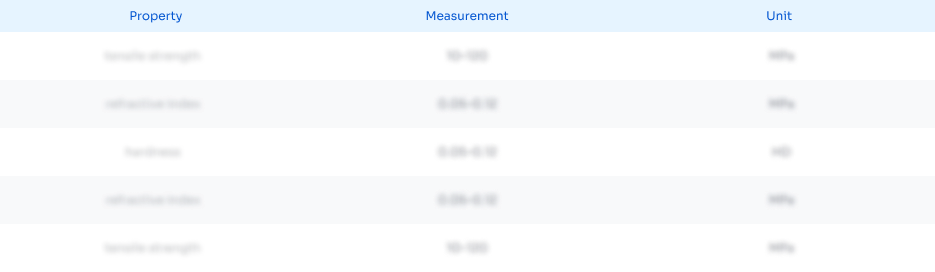
Abstract
Description
Claims
Application Information

- Generate Ideas
- Intellectual Property
- Life Sciences
- Materials
- Tech Scout
- Unparalleled Data Quality
- Higher Quality Content
- 60% Fewer Hallucinations
Browse by: Latest US Patents, China's latest patents, Technical Efficacy Thesaurus, Application Domain, Technology Topic, Popular Technical Reports.
© 2025 PatSnap. All rights reserved.Legal|Privacy policy|Modern Slavery Act Transparency Statement|Sitemap|About US| Contact US: help@patsnap.com