Method for machining shell liner of shell in semi-autogenous mill
A technology of semi-autogenous grinding machine and processing method, which is applied in the direction of metal processing equipment, manufacturing tools, furnace types, etc., and can solve the problems that affect the civilized production of modern enterprises, the lifting strip of the cylinder liner is weak, and cannot meet the time use requirements, etc. , to achieve the effect of optimizing the heat treatment process, improving the overall strength and hardness, good toughness and work hardening ability
- Summary
- Abstract
- Description
- Claims
- Application Information
AI Technical Summary
Problems solved by technology
Method used
Image
Examples
Embodiment Construction
[0027] Below in conjunction with accompanying drawing, the present invention will be further described;
[0028] The cylinder liner in the semi-autogenous mill includes the lower part 1 of the lifting bar, the lifting bar 2, and the upper part 3 of the lifting bar. To facilitate the lifting of the steel ball, the lower part 1 of the lifting bar is set at an obtuse angle, and reinforcing ribs 4 are symmetrically and evenly distributed on the upper part 3 of the lifting bar and the lower part 1 of the lifting bar, and hoisting holes 5 are arranged on the reinforcing rib 4 ribs.
[0029] The processing method of the cylinder liner in the semi-autogenous mill is characterized in that: ultra-high manganese alloy steel is used; the elements of the formula are, by weight percentage, carbon: 1.0~1.4, manganese: 17~19, phosphorus: <0.05, Silicon: 0.3~1.0, Sulfur: <0.05, Aluminum: <0.2, Vanadium: <0.5, Chromium: 1.5~2.5, Nickel: ≤1.5, Copper: ≤0.5~1, Molybdenum: 0.3~1.0, Rhenium: trace...
PUM
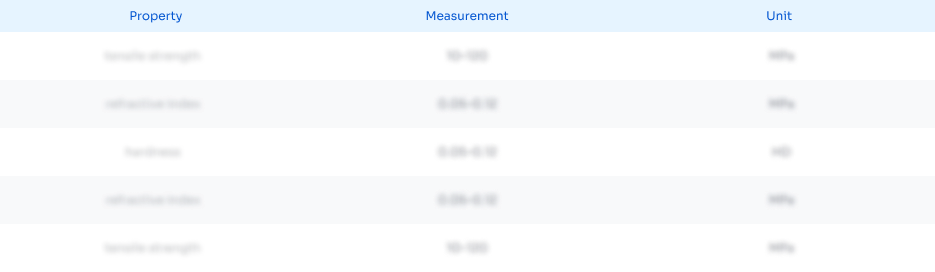
Abstract
Description
Claims
Application Information

- R&D
- Intellectual Property
- Life Sciences
- Materials
- Tech Scout
- Unparalleled Data Quality
- Higher Quality Content
- 60% Fewer Hallucinations
Browse by: Latest US Patents, China's latest patents, Technical Efficacy Thesaurus, Application Domain, Technology Topic, Popular Technical Reports.
© 2025 PatSnap. All rights reserved.Legal|Privacy policy|Modern Slavery Act Transparency Statement|Sitemap|About US| Contact US: help@patsnap.com