Method for controlling temperature rise in secondary combustion of vacuum refining exhaust gas
A technology of secondary combustion and temperature rise control, applied in the field of continuous casting control, can solve the problems of inability to carry out large-flow baking, long cold steel cycle, and long time to replace hot bending pipes.
- Summary
- Abstract
- Description
- Claims
- Application Information
AI Technical Summary
Problems solved by technology
Method used
Image
Examples
Embodiment Construction
[0014] The technical solutions of the present invention will be further described below in conjunction with the accompanying drawings and embodiments.
[0015] First, let me introduce the principle of secondary combustion of RH waste gas: in the multifunctional RH vacuum refining process, in order to increase the decarburization rate of molten steel, people will try to blow oxygen in the RH vacuum tank (that is, RH-KTB), through the oxygen stream The impact on the liquid steel surface in the vacuum chamber and the oxidation on the surface of the splashed steel droplets provide sufficient oxygen to the molten steel, thereby accelerating the decarburization speed. At the same time, the CO and H2 combustible gases removed from the molten steel meet the oxygen stream countercurrently, which meets the basic conditions for secondary combustion. The temperature of molten steel in the tank and the temperature in the vacuum tank can be increased through secondary combustion.
[0016] s...
PUM
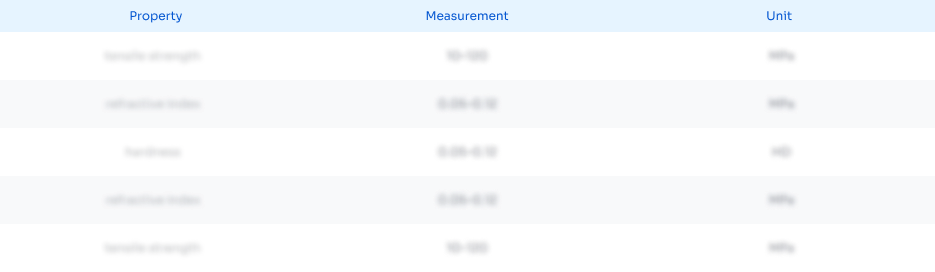
Abstract
Description
Claims
Application Information

- Generate Ideas
- Intellectual Property
- Life Sciences
- Materials
- Tech Scout
- Unparalleled Data Quality
- Higher Quality Content
- 60% Fewer Hallucinations
Browse by: Latest US Patents, China's latest patents, Technical Efficacy Thesaurus, Application Domain, Technology Topic, Popular Technical Reports.
© 2025 PatSnap. All rights reserved.Legal|Privacy policy|Modern Slavery Act Transparency Statement|Sitemap|About US| Contact US: help@patsnap.com