Control method of medium-thickness plate rolling and conveying speed
A control method and conveying speed technology, applied in the direction of roller speed control, etc., can solve problems such as not meeting the process requirements
- Summary
- Abstract
- Description
- Claims
- Application Information
AI Technical Summary
Problems solved by technology
Method used
Image
Examples
Embodiment
[0197] The medium and heavy plate production line is arranged in the order of finishing mill, pre-straightening machine and control cooling device. The roller table group is divided into 6 groups, and the names of each roller table group are FX1, FX2, FX3, FX4, FX5, AC1, FX5 The connection position with AC1 is the position of the first junction point, and the first junction point is far from the finishing mill S f is 58 meters, the distance S between the first junction point and the second junction point L is 5 meters, and the distance Sa from the second junction point to the control cooling device inlet is defined as 1.8 meters. Define the connection point between FX1 and FX2 as the transition point of the transport process.
[0198] Added speed control module C2 for globally coordinated calculation of speed map parameters g . Change C2 f , C1, C1a, C2a, increase the communication with C2g and change the original speed control function. Through the above addition and rec...
PUM
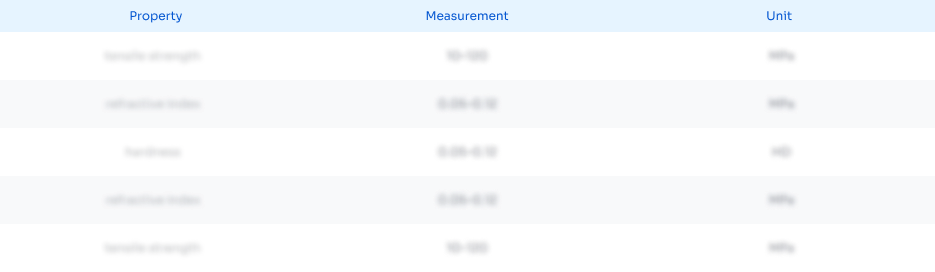
Abstract
Description
Claims
Application Information

- R&D
- Intellectual Property
- Life Sciences
- Materials
- Tech Scout
- Unparalleled Data Quality
- Higher Quality Content
- 60% Fewer Hallucinations
Browse by: Latest US Patents, China's latest patents, Technical Efficacy Thesaurus, Application Domain, Technology Topic, Popular Technical Reports.
© 2025 PatSnap. All rights reserved.Legal|Privacy policy|Modern Slavery Act Transparency Statement|Sitemap|About US| Contact US: help@patsnap.com