Technique for rolling figured steel for magnetic suspension train rail
A technology for magnetic levitation trains and special-shaped steel, applied in metal rolling, manufacturing tools, metal rolling, etc., can solve problems such as high cost, low efficiency, and complicated process, so as to improve production efficiency, meet mass production, and reduce costs Effect
- Summary
- Abstract
- Description
- Claims
- Application Information
AI Technical Summary
Problems solved by technology
Method used
Examples
Embodiment 1
[0025] Rectangular blanks are cold-loaded or hot-loaded into the furnace, heated to 1200-1230°C, and descaled by high-pressure water. In order to ensure the descaling effect, the descaling pressure is 10MPa. The rolling temperature is 1150-1180°C, and the final rolling temperature is 1000-1050°C. In order to ensure the uniformity of the structure of the product, a two-roll reversing mill is used for large deformation rolling at this stage. The maximum rolling force of the two-roll reversing mill is 8000KN. The amount of deformation should account for 65% of the total deformation. After the BD rolling is completed, the rough rolling billet is sent to the TM universal unit for continuous rolling through the conveying roller after the machine. two-roll rolling. The rolling force of the finish rolling is 10000KN, and the reduction accuracy is ±0.1mm; the starting rolling temperature is 800-850°C, and the final rolling temperature is 750-800°C, and the rest of the deformation is c...
Embodiment 2
[0029] Rectangular blanks are cold-loaded or hot-loaded into the furnace, heated to 1260-1280°C, and descaled by high-pressure water. In order to ensure the descaling effect, the descaling pressure is 20MPa. Rolling at 1180-1200°C, and final rolling temperature at 950-1000°C. In order to ensure the uniformity of the structure of the product, a two-roll reversible rolling mill is used for large deformation rolling at this stage. The maximum rolling force of the two-roll reversing rolling mill is 10000KN. The rolling deformation should account for 85% of the total deformation. After the BD rolling is completed, the rough rolling billet is sent to the TM universal unit for continuous rolling through the conveying roller after the machine. two-roll rolling. The rolling force of the finishing rolling is 13000KN, and the rolling precision is ±0.1mm; the starting rolling temperature is 850-900°C, and the final rolling temperature is 800-850°C, and the rest of the deformation is comp...
Embodiment 3
[0033] Rectangular blanks are cold-loaded or hot-loaded into the furnace, heated to 1240-1260°C, and descaled by high-pressure water. In order to ensure the descaling effect, the descaling pressure is 30MPa. The rolling temperature is 1210-1240°C, and the final rolling temperature is 1050-1100°C. In order to ensure the uniformity of the structure of the product, a two-roll reversible rolling mill is used for large deformation rolling at this stage. The maximum rolling force of the two-roll reversing rolling mill is 9000KN. The rolling deformation should account for 70% of the total deformation. After the BD rolling is completed, the rough rolling billet is sent to the TM universal unit for continuous rolling through the conveying roller after the machine. two-roll rolling. The rolling force of the finish rolling is 12000KN, and the reduction accuracy is ±0.1mm; the starting rolling temperature is 900-1000°C, and the final rolling temperature is 750-800°C. The rest of the defo...
PUM
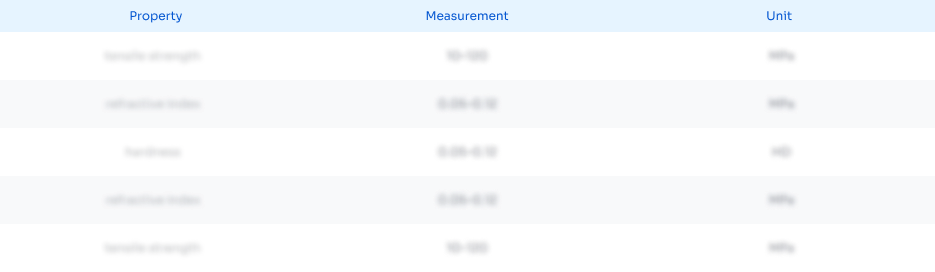
Abstract
Description
Claims
Application Information

- R&D
- Intellectual Property
- Life Sciences
- Materials
- Tech Scout
- Unparalleled Data Quality
- Higher Quality Content
- 60% Fewer Hallucinations
Browse by: Latest US Patents, China's latest patents, Technical Efficacy Thesaurus, Application Domain, Technology Topic, Popular Technical Reports.
© 2025 PatSnap. All rights reserved.Legal|Privacy policy|Modern Slavery Act Transparency Statement|Sitemap|About US| Contact US: help@patsnap.com