Nickel molybdenum titanium intermediate alloy and preparation method thereof
A master alloy, nickel-molybdenum technology, applied in the field of nickel-molybdenum-titanium master alloy and its preparation, can solve the problems of high density, affect the performance of titanium alloy, and high melting point of metal molybdenum, and achieve simple production process, stable product quality, and uniform element distribution. Effect
- Summary
- Abstract
- Description
- Claims
- Application Information
AI Technical Summary
Problems solved by technology
Method used
Image
Examples
Embodiment 1
[0018] Step 1: Calculate according to the target composition of the nickel-molybdenum-titanium master alloy, the feeding amount is 15kg, and weigh the required weight of 10.5kg of electrolytic nickel, 4.43kg of molybdenum slab, and 0.07kg of titanium sponge.
[0019] Step 2: Place the electrolytic nickel and molybdenum slabs in the crucible of the intermediate frequency induction furnace in sequence, and place the titanium sponge in the gap between the above two raw materials.
[0020] Step 3: When the vacuum degree is 20Pa, the intermediate frequency induction furnace is powered, the initial power is 10kw, and the maximum power does not exceed 50kw. After all the materials are melted, overheat for 5 minutes and power off, and cast into cylindrical ingots when the temperature drops to 1300~1350°C.
[0021] Step 4: Sampling the upper and lower parts of the ingot for chemical composition analysis. The analysis results of the upper and lower parts are shown in the table below. ...
Embodiment 2
[0025] Step 1: Calculate according to the target composition of the nickel-molybdenum-titanium master alloy, the feeding amount is 13kg, and the required weight is 9.1kg of nickel scrap, 3.83kg of molybdenum scrap, and 0.07kg of pure titanium scrap.
[0026] Step 2: place nickel scraps and molybdenum scraps in the crucible of the intermediate frequency induction furnace in sequence, and add pure titanium scraps to the gap between the above two raw materials.
[0027] Step 3: When the vacuum degree is 15Pa, the intermediate frequency induction furnace is powered, the initial power is 10kw, and the maximum power does not exceed 50kw. After the material is completely melted, it is overheated for 6 minutes and the power is turned off. When the temperature drops to 1300~1350°C, it is cast into a cylindrical ingot.
[0028] Step 4: Sampling the upper and lower parts of the ingot for chemical composition analysis. The analysis results are shown in the table below. The analysis resu...
PUM
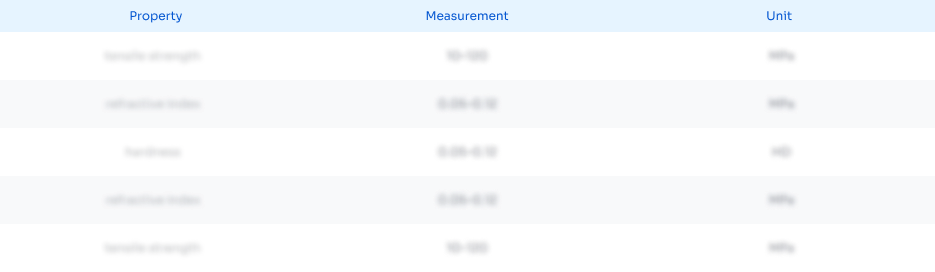
Abstract
Description
Claims
Application Information

- Generate Ideas
- Intellectual Property
- Life Sciences
- Materials
- Tech Scout
- Unparalleled Data Quality
- Higher Quality Content
- 60% Fewer Hallucinations
Browse by: Latest US Patents, China's latest patents, Technical Efficacy Thesaurus, Application Domain, Technology Topic, Popular Technical Reports.
© 2025 PatSnap. All rights reserved.Legal|Privacy policy|Modern Slavery Act Transparency Statement|Sitemap|About US| Contact US: help@patsnap.com