A kind of preparation method of fine-grain/ultra-fine-grain metal layered material
A metal material and metal layer technology, applied in the direction of metal extrusion dies, etc., can solve problems such as total strain limit, material strength reduction, material size reduction, etc., to achieve low equipment requirements, good stress state, and refinement of grains. Effect
- Summary
- Abstract
- Description
- Claims
- Application Information
AI Technical Summary
Problems solved by technology
Method used
Image
Examples
Embodiment 1
[0045] figure 1 Schematic diagram of the unequal channel angular extrusion die used in this example. Such as figure 1 As shown, the non-equal channel angular extrusion die is provided with intersecting first channel 1 and second channel 2, and the first channel 1 and second channel 2 form a corner, wherein the internal angle Φ is 120° (the value range can be 90°~160°), the outer angle Ψ is 45° (the value range can be 0°~45°); the width W of the first channel 1 and the second channel 2 are equal, W=50mm, the thickness L of the first channel 1 =20mm, greater than the thickness L of the second channel 2 =10mm; that is, the cross-sectional dimension of the first channel 1 is 20mm×50mm (L 1 ×W), the cross-sectional size of the first channel 2 is 10mm×50mm (L 2 ×W).
[0046] In this embodiment, the same metal layered material is prepared, and the specific steps are as follows:
[0047] (1) Select two metal material samples, and pretreat the superimposed surfaces of the metal m...
Embodiment 2
[0057] In this embodiment, heterogeneous metal layered materials are prepared, and the specific steps are as follows:
[0058] (1) Select two metal material samples, and pretreat the superimposed surfaces of the metal material samples: remove the attachments and oxides on the superimposed surfaces by mechanical grinding or chemical methods;
[0059] The two metal material samples in this embodiment are hot-rolled ME20M magnesium alloy plate and pure aluminum ingot (99.7%), the cross-sectional dimensions are 10mm×50mm, and the composition of ME20M magnesium alloy plate is the same as that in Example 1.
[0060] (2) Multi-pass composite extrusion:
[0061] The first compound extrusion:
[0062] (2-1) After superimposing the metal material samples to form a combined sample, wrap the combined sample with aluminum foil and place it in the first channel of the non-equal channel angular extrusion die. At the same time, the non-equal channel angular extrusion The mold is preheated; ...
Embodiment 3
[0073] Present embodiment except following steps, all the other steps are all the same with embodiment 2:
[0074] (2-5) After superimposing the pretreated metal material samples along the thickness direction, wrap them with aluminum foil, rotate 180°, and place them in the first channel of the non-equal channel angular extrusion die. At the same time, the non-equal channel The corner extrusion die is preheated;
[0075] (2-6) Extrusion deformation: after 400°C, keep warm for 60 minutes, apply extrusion force immediately after the holding time is up, and make the metal material sample completely pass through the first channel of the non-equal channel angular extrusion die at a speed of 1.5mm / s and the corner of the second channel, extruded through the second channel.
[0076] In this embodiment, the layered material of dissimilar metals is obtained, which has good interfacial bonding.
PUM
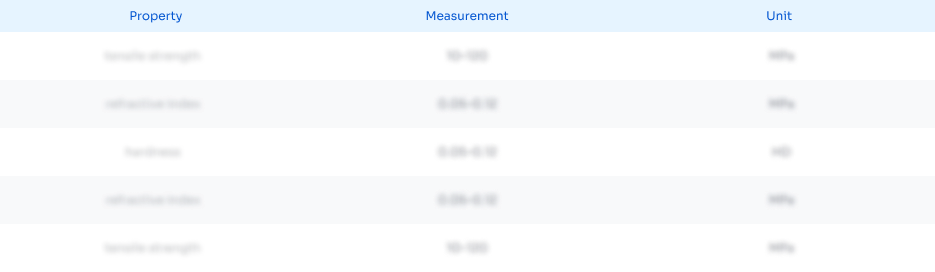
Abstract
Description
Claims
Application Information

- Generate Ideas
- Intellectual Property
- Life Sciences
- Materials
- Tech Scout
- Unparalleled Data Quality
- Higher Quality Content
- 60% Fewer Hallucinations
Browse by: Latest US Patents, China's latest patents, Technical Efficacy Thesaurus, Application Domain, Technology Topic, Popular Technical Reports.
© 2025 PatSnap. All rights reserved.Legal|Privacy policy|Modern Slavery Act Transparency Statement|Sitemap|About US| Contact US: help@patsnap.com