Hydrogen storing alloy for rare earth capacitor battery and preparation method thereof
A technology for capacitor batteries and hydrogen storage alloys, which is applied in the field of hydrogen storage alloys for rare earth capacitor batteries and its preparation, can solve problems such as poor dispersion, small area of sintered pole pieces, and reduced flexibility, so as to reduce the segregation degree of alloy components and improve Improvement of internal space utilization and reaction dynamics
- Summary
- Abstract
- Description
- Claims
- Application Information
AI Technical Summary
Problems solved by technology
Method used
Image
Examples
Embodiment 1
[0036] a. Mix the raw materials with the mass ratio of La21%, Ce8.5%, Pr1%, Nd2.3%, Ni55%, Co6.5%, Mn3.5%, Al2.2%, La, Ce, Pr and Nd Recycled battery grade mixed rare earth materials, Ni is recycled nickel foam, Co is cobalt block, Mn is manganese metal sheet, Al is metal aluminum block, raw material purity ≥ 99.5%, vacuum induction melting, the vacuum induction furnace is evacuated to 3.2╳10 -3 Pa, and then introduce argon until the pressure in the furnace is -0.04±0.01MPa, and the melting temperature is 1000±100°C. After the smelting is completed, it is poured into a copper water-cooled mold for cooling at a cooling rate of 110±10K / s to obtain an alloy ingot.
[0037] b, put the alloy ingot at room temperature for 10 days;
[0038] c. Adding nanoscale Co with a mass fraction of 0.5% of the raw material 3 o 4 and nanoscale CeO 2 , where nanoscale Co 3 o 4 and nanoscale CeO 2 The mass ratio of the alloy is 1:1. Under the argon atmosphere, the supersonic argon jet mill ...
Embodiment 2
[0042] a. Mix raw materials with a mass ratio of La20.5%, Ce8.3%, Pr0.9%, Nd2.5%, Ni57%, Co6%, Mn3%, Al1.8%, La, Ce, Pr and Nd It is a battery grade mixed rare earth material, Ni is a nickel block, Co is a cobalt block, Mn is a manganese metal sheet, and Al is a metal aluminum block. The purity of the raw material is ≥99.5%. Vacuum induction melting, the vacuum induction furnace is evacuated to 2.5╳10 -3 Pa, and then introduce argon until the pressure in the furnace is -0.03±0.01MPa, and the melting temperature is 1400±100°C. After the smelting is completed, it is poured into a copper water-cooled mold for cooling at a cooling rate of 150±10K / s to obtain an alloy ingot.
[0043] b. Shelve the alloy ingot at room temperature for 30 days;
[0044] c. Adding mass fraction of 3% nanometer Co 3 o 4 and nanoscale CeO 2 , where nanoscale Co 3 o 4 and nanoscale CeO 2 The mass ratio of the alloy is 1:2. Under the argon atmosphere, the supersonic argon jet mill is used to pulveri...
Embodiment 3
[0048] a, La21.5%, Ce8.7%, Pr1.1%, Nd2.7%, Ni53%, Co7%, Mn4%, Al2% raw materials mixed, La, Ce, Pr and Nd are battery grade mixed rare earth materials , and recovered materials (accounting for 50% by mass ratio), Ni is nickel block and recycled nickel foam (each accounts for 50% by mass ratio), Co is cobalt block, Mn is metal manganese sheet, Al is metal aluminum block, and the purity of raw materials ≥99.5%, vacuum induction melting, vacuum the vacuum induction furnace to 2.8╳10 -3 Pa, and then feed argon until the pressure in the furnace is -0.05±0.01MPa, and the melting temperature is 1600±100°C. After the smelting is completed, it is poured into a copper water-cooled mold for cooling at a cooling rate of 200±10K / s to obtain an alloy ingot.
[0049] B, put the alloy ingot at room temperature for 20 days;
[0050] c. Adding a mass fraction of 2% nanoscale Co to the raw material 3 o 4 and nanoscale CeO 2 , where nanoscale Co 3 o 4 and nanoscale CeO 2 The mass ratio of...
PUM
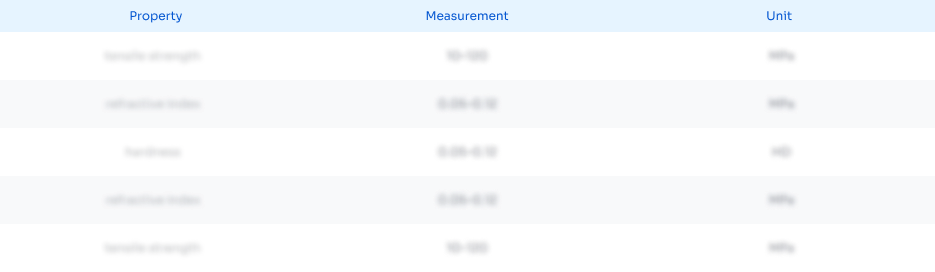
Abstract
Description
Claims
Application Information

- Generate Ideas
- Intellectual Property
- Life Sciences
- Materials
- Tech Scout
- Unparalleled Data Quality
- Higher Quality Content
- 60% Fewer Hallucinations
Browse by: Latest US Patents, China's latest patents, Technical Efficacy Thesaurus, Application Domain, Technology Topic, Popular Technical Reports.
© 2025 PatSnap. All rights reserved.Legal|Privacy policy|Modern Slavery Act Transparency Statement|Sitemap|About US| Contact US: help@patsnap.com