Halogen-free flame retardant polypropylene composition
A flame-retardant polypropylene and composition technology, applied in the field of polypropylene composition, can solve problems such as processing difficulties, achieve the effects of easy demolding, avoid migration, and improve demolding and surface quality
- Summary
- Abstract
- Description
- Claims
- Application Information
AI Technical Summary
Problems solved by technology
Method used
Image
Examples
Embodiment 1
[0089] Weigh polypropylene resin S1003, magnesium hydroxide MAGNIFINH-5IV, pentaerythritol, polyester modified polydimethylsiloxane respectively according to the ratio shown in Table 2 H-Si6440P, talcum powder 8860, elastomer Engage8100, compatibilizer GPM200AL and black masterbatch are pre-mixed uniformly with a high-speed mixing and stirring device at room temperature, and the mixture is quantitatively transported from the main hopper to the main feed of the co-rotating twin-screw extruder In the feed port, melt extrusion is carried out, the extrusion temperature is 220°C, and the rotation speed is 300rpm. After the extruded strands are cooled in a water tank, they are cut into pellets with a length of about 3mm by a pelletizer. After the pellets are dried at 120°C for 6 hours, Injection molded into a standard sample bar with an injection molding machine, and carried out the determination of UL94, CTI (V), scratch resistance and migration resistance, the results are shown in...
Embodiment 2
[0091] Weigh polypropylene resin S1003, polypropylene resin K1003, magnesium hydroxide MAGNIFINH-5IV, dipentaerythritol, tripentaerythritol, and polyolefin modified polydimethylsiloxane masterbatches according to the proportions shown in Table 2. FR100 and black masterbatch are pre-mixed uniformly with a high-speed mixing and stirring device at room temperature, and the mixture is quantitatively transported from the main hopper to the main feeding port of the co-rotating twin-screw extruder, and the glass fiber ER13-2000-910 is quantitatively fed through the side Introduce and carry out melt extrusion, the extrusion temperature is 220°C, the speed is 300rpm, the extruded strands are cooled in a water tank, and then cut into pellets with a length of about 3mm by a pelletizer. After the pellets are dried at 120°C for 6 hours, use The injection molding machine was injected into standard strips, and the measurements of UL94, CTI(V), scratch resistance and migration resistance were...
Embodiment 3
[0093] Weigh polypropylene resin K1003 and polyester modified polydimethylsiloxane respectively according to the ratio shown in Table 2 H-Si6440P, polyether modified polysiloxane 6875, tripentaerythritol, magnesium hydroxide MAGNIFINH-5IV, talcum powder 8860, elastomer Engage8100, compatibilizer GPM200AL and black masterbatch are pre-mixed uniformly with a high-speed mixing device at room temperature, and the mixture is quantitatively transported from the main hopper to the same Melt extrusion into the main feeding port of the twin-screw extruder, the extrusion temperature is 220°C, the rotation speed is 300rpm, the extruded strands are cooled in a water tank, and then cut into pellets with a length of about 3mm by a pelletizer. After drying at 120°C for 6 hours, it was molded into a standard sample with an injection molding machine, and tested for UL94, CTI(V), scratch resistance and migration resistance. The results are shown in Table 2.
PUM
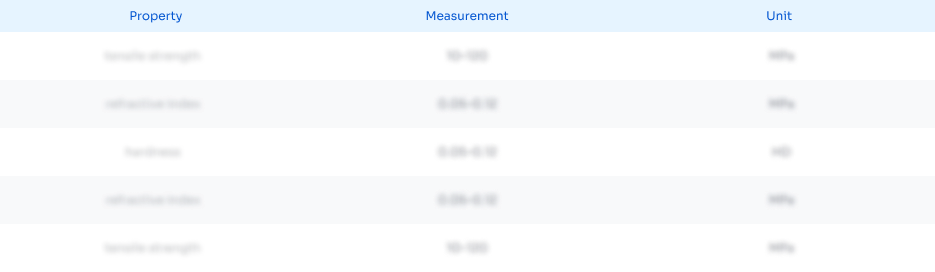
Abstract
Description
Claims
Application Information

- R&D Engineer
- R&D Manager
- IP Professional
- Industry Leading Data Capabilities
- Powerful AI technology
- Patent DNA Extraction
Browse by: Latest US Patents, China's latest patents, Technical Efficacy Thesaurus, Application Domain, Technology Topic, Popular Technical Reports.
© 2024 PatSnap. All rights reserved.Legal|Privacy policy|Modern Slavery Act Transparency Statement|Sitemap|About US| Contact US: help@patsnap.com