Preparation method for antifouling paint matrix resin containing ionic liquid perssads
A technology for antifouling coatings and matrix resins, applied in antifouling/underwater coatings, biocide-containing paints, coatings, etc. To avoid problems such as poor biological attachment, to achieve good eco-friendliness, good antifouling activity, and the effect of inhibiting marine biological attachment
- Summary
- Abstract
- Description
- Claims
- Application Information
AI Technical Summary
Problems solved by technology
Method used
Image
Examples
preparation example Construction
[0029] Preparation of hydrophobic ionic liquid monomer:
[0030] Add 82 grams of N-methylimidazole, 165 grams of chloromethylstyrene, and 0.5 grams of polymerization inhibitor 2,6-di-tert-butyl-p-cresol (DBMP) into a reaction flask. Under the protection of nitrogen, stir at a constant temperature of 35°C for 24 hours to form a yellowish viscous liquid, wash with ether, and dry under vacuum at room temperature overnight to obtain a transparent, viscous liquid 1-(4-vinylbenzyl-)-3-methylimidazole chlorine. Then 18 grams of ammonium hexafluorophosphate or 12.1 grams of sodium tetrafluoroborate and 100 ml of acetone were mixed evenly and then added to 27.6 grams of 1-(4-vinylbenzyl-)-3-methylimidazole chloride, 0.2 grams of polymerization inhibitor DBMP , 100ml of acetone, stirred at 30°C for 24 hours, then filtered, and the filtrate was distilled under reduced pressure to obtain a white waxy solid. The crude product was washed with water and ether and stored for later use.
Embodiment 1
[0032] First, 32 parts of toluene and n-butanol mixed solvent with a mass ratio of 4:1 were added to a reaction flask equipped with a condenser tube and a dropping funnel, and the temperature was controlled at 90°C. methyl acrylate, 17 parts of n-butyl acrylate, 6 parts of ethyl acrylate, 9 parts of acrylic acid, 3 parts of silicone monomer, 4 parts of hydrophobic ionic liquid monomer, 0.8 part of azobisisobutyronitrile, 0.5 part of ten The mixed solution of dithiol was controlled to be dripped within 1.5 hours, and was incubated for 2 hours. Then add 0.2 parts of remaining mixed solvent dissolved in azobisisobutyronitrile within 0.5 hour, and keep warm for 1 hour to obtain an acrylic acid prepolymer containing ionic liquid groups. Subsequently, 46 parts of acrylic acid prepolymers containing ionic liquid groups, 5.7 parts of zinc hydroxide, and 20 parts of xylene and butyl acetate mixed solvents with a mass ratio of 1; In the reaction bottle of the separator, dissolve 8 part...
Embodiment 2
[0034] The synthesis of the acrylic acid prepolymer containing ionic liquid groups in this example is the same as in Example 1. Add 45 parts of acrylic acid prepolymer containing ionic liquid groups, 5.5 parts of zinc hydroxide, 20 parts of xylene and butyl acetate mixed solvent with a mass ratio of 1; In the reaction bottle of the reactor, dissolve 12.4 parts of perfluorooctanoic acid and 3.2 parts of benzoic acid in 14 parts of mixed solvent, control the temperature at 95 ° C, and evenly add the above mixed solution of organic acids dropwise under nitrogen purging, and keep the reflux state until the reaction solution is transparent. Then heat up to 125°C for dehydration until the water is completely removed to obtain a transparent, clear, viscous antifouling coating matrix resin containing ionic liquid groups.
PUM
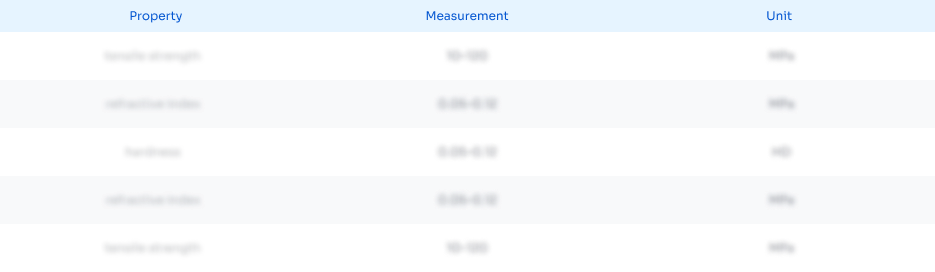
Abstract
Description
Claims
Application Information

- R&D Engineer
- R&D Manager
- IP Professional
- Industry Leading Data Capabilities
- Powerful AI technology
- Patent DNA Extraction
Browse by: Latest US Patents, China's latest patents, Technical Efficacy Thesaurus, Application Domain, Technology Topic, Popular Technical Reports.
© 2024 PatSnap. All rights reserved.Legal|Privacy policy|Modern Slavery Act Transparency Statement|Sitemap|About US| Contact US: help@patsnap.com