Graphene reinforcing and toughening nylon resin and preparation method thereof
A nylon resin, reinforced and toughened technology, applied in the field of graphene reinforced and toughened nylon resin and its preparation, can solve the problems of increased thermal conductivity, reduced thermal expansion coefficient, large usage, etc., to achieve increased aggregation, improved uniform dispersion, The effect of low electrical performance
- Summary
- Abstract
- Description
- Claims
- Application Information
AI Technical Summary
Problems solved by technology
Method used
Image
Examples
Embodiment 1-4
[0017] Embodiment 1-4 (unit: %)
[0018]
[0019] Nylon 6 is dried in a drying hopper at 90-110°C for 3 to 4 hours, and the formula amount of nylon 6 (PA6), phosphorus nitrogen type nylon flame retardant (DS-1), and various additives are mixed in a high-speed mixing hopper After mixing evenly, add it from the mixing port into the twin-screw extruder with the temperature set at 225-275°C, the length-to-diameter ratio (L / D) of 32:1-40:1, and the screw combination according to the process regulations. Vacuum granulation to make graphene nano-modified reinforced nylon 6 resin. The sampled material was dried at 90-110°C for 3-4 hours and then injection molded into a standard sample for performance testing. The performance is shown in Table 2.
[0020] The performance test result of table two embodiment 1-4
[0021]
Embodiment 5-8
[0022] Embodiment 5-8 (unit: %)
[0023]
[0024] Nylon 66 is dried in a drying hopper at 90-110°C for 3-4 hours, and the formula amount of nylon 6 (PA6), phosphorus-nitrogen synergistic nylon flame retardant (DS-1), modified graphene, various After the additives are mixed evenly in the high-speed mixing bucket as required, add them from the mixing port until the temperature is set at 230-280°C, the length-to-diameter ratio (L / D) is 32:1-40:1, and the screw combination is according to the process regulations. In a twin-screw extruder, vacuum granulation is used to make halogen-free glass fiber reinforced nylon 66 resin. The sampled material was dried at 90-110°C for 3-4 hours and then injection molded into a standard sample for performance testing. The performance is shown in Table 4.
[0025] The performance test result of table four embodiment 5-8
[0026]
[0027]
[0028] The amount and distribution of nylon 66 (PA66) or nylon 6 (PA6) in the above-mentioned exam...
PUM
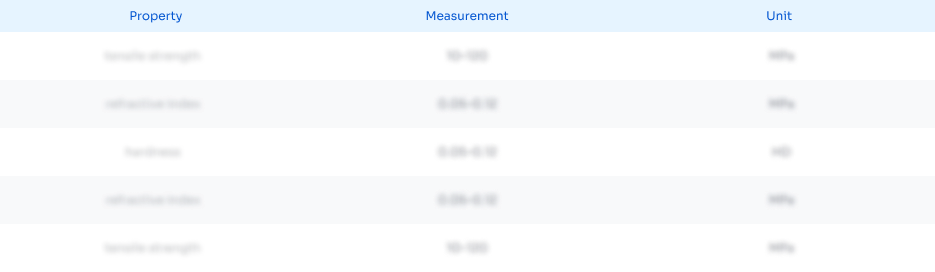
Abstract
Description
Claims
Application Information

- Generate Ideas
- Intellectual Property
- Life Sciences
- Materials
- Tech Scout
- Unparalleled Data Quality
- Higher Quality Content
- 60% Fewer Hallucinations
Browse by: Latest US Patents, China's latest patents, Technical Efficacy Thesaurus, Application Domain, Technology Topic, Popular Technical Reports.
© 2025 PatSnap. All rights reserved.Legal|Privacy policy|Modern Slavery Act Transparency Statement|Sitemap|About US| Contact US: help@patsnap.com