Method for preparing heavy high-purity basic cupric carbonate
A copper carbonate and soda ash technology, applied in chemical instruments and methods, copper compounds, inorganic chemistry, etc., can solve the problem that the product fineness and precision cannot meet market requirements, pressure changes increase production difficulties, and affect the yield of basic copper carbonate. and other problems, to achieve the effect of avoiding direct steam discharge, low cost, and avoiding reprocessing procedures
- Summary
- Abstract
- Description
- Claims
- Application Information
AI Technical Summary
Problems solved by technology
Method used
Examples
Embodiment 1
[0024] (1) Pour liquid ammonia into the water at a pressure of 0.2MPa, pass the ammonia for 6 hours to produce concentrated ammonia water with a concentration of 135g / L, then pass carbon dioxide with a purity ≥ 99.9% into the concentrated ammonia water to prepare carbonized ammonia water, and turn on the cooling at the same time Water, pass cooling water with a temperature lower than 15°C into the cooling coil installed in the concentrated ammonia water but not connected with the concentrated ammonia water, and control the pressure of carbon dioxide to be 0.2MPa, so that the degree of carbonization is 160%;
[0025] (2) Put 62.5×10 in an airtight container 3 mol copper content ≥ 99.95% standard cathode copper, and then inject 3 m into the container 3 The carbonized ammonia water prepared in step (1) is reacted, and air is blown into the container at the same time, so that the air pressure in the container is 10×10 5 Pa, the time of blowing into the air is 12 hours, when the c...
Embodiment 2
[0031] (1) Pour liquid ammonia into the water at a pressure of 0.1MPa, pass the ammonia for 7 hours to produce concentrated ammonia water with a concentration of 120g / L, then pass carbon dioxide with a purity ≥ 99.9% into the concentrated ammonia water to prepare carbonized ammonia water, and turn on the cooling at the same time Water, pass cooling water with a temperature lower than 15°C into the cooling coil installed in the concentrated ammonia water but not connected with the concentrated ammonia water to cool, control the pressure of passing carbon dioxide to 0.1MPa, and make the degree of carbonization 140%;
[0032] (2) Put 62.5×10 in an airtight container 3 mol copper content ≥ 99.95% standard cathode copper, then inject 3.5 m into the container 3 The carbonized ammonia water prepared in step (1) is reacted, and air is blown into the container at the same time, so that the air pressure in the container is 5×10 5 Pa, the time for blowing air is 8 hours, stop blowing ai...
Embodiment 3
[0038] (1) Pass liquid ammonia into the water at a pressure of 0.05MPa, pass the ammonia for 5 hours to produce concentrated ammonia water with a concentration of 85g / L, then pass carbon dioxide with a purity ≥ 99.9% into the concentrated ammonia water to prepare carbonized ammonia water, and turn on the cooling at the same time Water, pass cooling water with a temperature lower than 15°C into the cooling coil installed in the concentrated ammonia water but not connected with the concentrated ammonia water, and control the pressure of carbon dioxide to be 0.05MPa, so that the degree of carbonization is 80%;
[0039] (2) Put 62.5×10 in an airtight container 3 mol copper content ≥ 99.95% standard cathode copper, then inject 3.2m into the container 3 The carbonized ammonia water prepared in step (1) is reacted, and air is blown into the container at the same time, so that the air pressure in the container is 1.01×10 5 Pa, the time for blowing air into it was 5 hours, and when th...
PUM
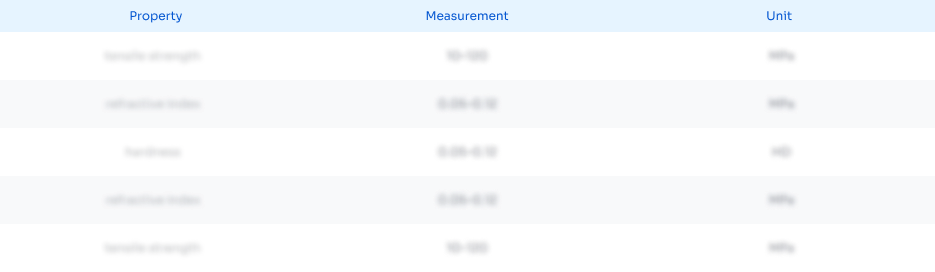
Abstract
Description
Claims
Application Information

- Generate Ideas
- Intellectual Property
- Life Sciences
- Materials
- Tech Scout
- Unparalleled Data Quality
- Higher Quality Content
- 60% Fewer Hallucinations
Browse by: Latest US Patents, China's latest patents, Technical Efficacy Thesaurus, Application Domain, Technology Topic, Popular Technical Reports.
© 2025 PatSnap. All rights reserved.Legal|Privacy policy|Modern Slavery Act Transparency Statement|Sitemap|About US| Contact US: help@patsnap.com