Extraction method of seaweed polysaccharide
A seaweed polysaccharide and extraction method technology, applied in the field of seaweed polysaccharide extraction, can solve the problems of long cycle, destruction of effective components, low extraction rate, etc., and achieve the effects of simple method, small damage and improved extraction efficiency
- Summary
- Abstract
- Description
- Claims
- Application Information
AI Technical Summary
Problems solved by technology
Method used
Examples
Embodiment 1
[0028] (1) After washing the raw materials of kelp and sargassum with clean water, dry them at 30°C for 12 hours. The water content of the raw materials is about 12%; then crush the raw materials and pass through a 60-mesh sieve;
[0029] (2) Add distilled water to the sieved pulverized matter at a solid-to-liquid ratio of 1:25 for ultra-high pressure extraction, pressurize at 200 MPa, and temperature at 30°C; hold the pressure for 3 minutes, and filter with suction to obtain the filtrate to obtain the crude seaweed polysaccharide extract;
[0030] (3) Add activated carbon to the crude extract so that the mass percentage of the crude extract and activated carbon is 0.6%, decolorize for 30 minutes, and filter to obtain a mixed solution;
[0031] (4) The mixed solution is concentrated by vacuum rotary evaporation, and the seaweed polysaccharide mixed solution is concentrated to a mass concentration of 70% at a temperature of 50°C and a vacuum of 10KPa; then the concentrated solut...
Embodiment 2
[0033] (1) Wash the macroalgae and Ascophyllum nodosum raw materials with clean water, and dry them at 38°C for about 14 hours. The water content of the raw materials is about 10%; then crush the raw materials and pass through a 60-mesh sieve;
[0034] (2) Add distilled water to the sieved pulverized matter at a solid-to-liquid ratio of 1:28 for ultra-high pressure extraction, pressurize at 267 MPa, and temperature at 43°C; hold the pressure for 4.7 minutes, and filter with suction to obtain the filtrate to obtain the crude seaweed polysaccharide extract;
[0035] (3) Add activated carbon to the crude extract so that the mass percentage of the crude extract and activated carbon is 1.5%, decolorize for 45 minutes, and filter to obtain a mixed solution;
[0036] (4) The mixed solution is concentrated by vacuum rotary evaporation. The seaweed polysaccharide mixed solution is concentrated to a mass concentration of 75.7% at a temperature of 66.7°C and a vacuum of 17KPa; then the co...
Embodiment 3
[0038] (1) Wash the raw materials of Ascophyllum nodosum and Fucus nodosum with clean water, and then dry them at 47°C for about 16 hours. The water content of the raw materials is about 8%. Then the raw material is pulverized and passed through a 60-mesh sieve;
[0039] (2) Add distilled water to the sieved pulverized matter at a solid-to-liquid ratio of 1:32 for ultra-high pressure extraction, pressurize at 334 MPa, and temperature at 57°C; keep the pressure for 6.4 minutes, and filter with suction to obtain the filtrate to obtain the crude seaweed polysaccharide extract;
[0040] (3) Add activated carbon to the crude extract so that the mass percentage of the crude extract and activated carbon is 2.4%, decolorize for 60 minutes, and filter to obtain a mixed solution;
[0041] (4) The mixed solution is concentrated by vacuum rotary evaporation. The seaweed polysaccharide mixed solution is concentrated to a mass concentration of 81.4% at a temperature of 83.4°C and a vacuum o...
PUM
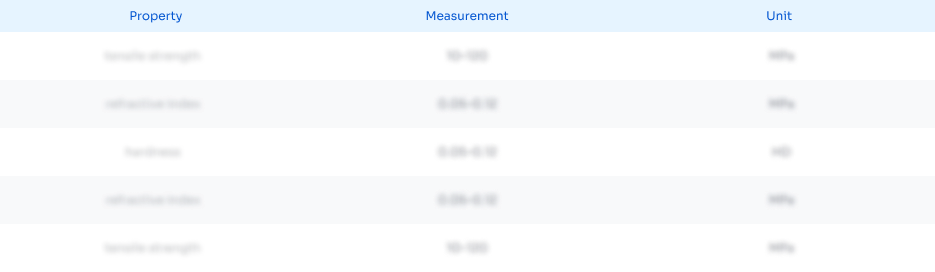
Abstract
Description
Claims
Application Information

- R&D
- Intellectual Property
- Life Sciences
- Materials
- Tech Scout
- Unparalleled Data Quality
- Higher Quality Content
- 60% Fewer Hallucinations
Browse by: Latest US Patents, China's latest patents, Technical Efficacy Thesaurus, Application Domain, Technology Topic, Popular Technical Reports.
© 2025 PatSnap. All rights reserved.Legal|Privacy policy|Modern Slavery Act Transparency Statement|Sitemap|About US| Contact US: help@patsnap.com