Casting method of air-cooled engine cylinder
An air-cooled engine and cylinder liner technology, applied in casting molding equipment, casting molds, casting mold components, etc., can solve problems such as energy conservation and environmental protection, mass production, complex process schemes, and low utilization of molten iron, and achieve production The effect of environment improvement, smooth appearance, and labor intensity reduction
- Summary
- Abstract
- Description
- Claims
- Application Information
AI Technical Summary
Problems solved by technology
Method used
Image
Examples
specific Embodiment approach 1
[0051] This embodiment adopts the casting method provided by the present invention to cast an air-cooled engine boron material cylinder liner with a weight of 6.8 kg, a temperature of molten iron of 1350 degrees, and a rotation speed of 1000 revolutions per minute. After the molten iron is poured into a double-layer mold, the automatic switch is started, and the time relay automatically It is controlled to start pumping water after 20 seconds of rotation, and the water pumping time is 40 seconds. After the water is stopped, continue to rotate for 60 seconds and then stop. The resin sand core inner mold and the cylinder liner blank of the air-cooled engine are ejected and put into a fixed insulation material box. After complete cooling, use a shot blasting machine to clean the sand to obtain the air-cooled engine cylinder liner blank.
specific Embodiment approach 2
[0052]This embodiment adopts the casting method provided by the present invention to cast an air-cooled engine phosphorus cylinder liner, with a weight of 5.2 kg, a temperature of molten iron of 1320 degrees, and a rotation speed of 1000 revolutions per minute. After the molten iron is poured into a double-layer mold, the automatic switch is started, and the time relay It is controlled to start pumping water after 20 seconds of rotation, and the water pumping time is 30 seconds. After the water is stopped, continue to rotate for 50 seconds and then stop. The resin sand core inner mold and the cylinder liner blank of the air-cooled engine are ejected and put into a fixed insulation material box. After complete cooling, use a shot blasting machine to clean the sand to obtain the air-cooled engine cylinder liner blank.
PUM
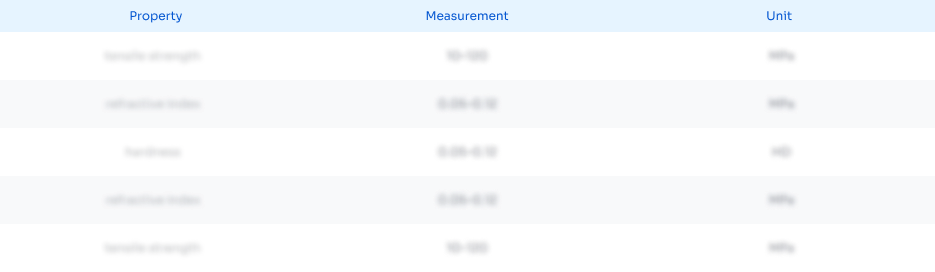
Abstract
Description
Claims
Application Information

- R&D
- Intellectual Property
- Life Sciences
- Materials
- Tech Scout
- Unparalleled Data Quality
- Higher Quality Content
- 60% Fewer Hallucinations
Browse by: Latest US Patents, China's latest patents, Technical Efficacy Thesaurus, Application Domain, Technology Topic, Popular Technical Reports.
© 2025 PatSnap. All rights reserved.Legal|Privacy policy|Modern Slavery Act Transparency Statement|Sitemap|About US| Contact US: help@patsnap.com