Method for preventing casting boss from shrinkage porosity
A boss and defect technology is applied in the field of preventing shrinkage porosity of casting bosses, which can solve the problems that metallurgical quality is difficult to meet the requirements of acceptance standards, casting shrinkage defects, and casting difficulty, etc., so as to reduce the risk of quality uncertainties, The effect of simplifying the process plan and reducing the cost of production materials
- Summary
- Abstract
- Description
- Claims
- Application Information
AI Technical Summary
Problems solved by technology
Method used
Image
Examples
Embodiment Construction
[0016] Below in conjunction with accompanying drawing, the present invention is described in further detail:
[0017] A method for preventing shrinkage and porosity defects of casting bosses of "igniter housing", mainly including the steps of wax mold part 1 pressing, shell making, pouring, boss 2 drilling, etc. After the wax mold part 1 is pressed, the A cooling part 3 is inserted into the center of the boss 2 of part 1, and then the gap between the boss 2 and the cooling part 3 is sealed with wax material. The radial dimension of the cooling part 3 is 6.5 mm, which is more finished than the boss 2 The final hole diameter is 0.4mm smaller, that is, to ensure that the cooling part 3 is completely removed after the hole at the boss is processed, the axial dimension of the cooling part 3 is 4.5mm longer than the thickness of the boss, so that the core head can be positioned well, and the cooling part 3 The material is a high temperature resistant material, such as ZGCr25Ni20 ste...
PUM
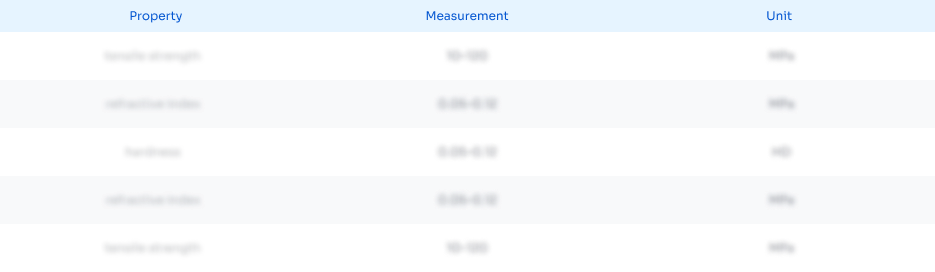
Abstract
Description
Claims
Application Information

- R&D
- Intellectual Property
- Life Sciences
- Materials
- Tech Scout
- Unparalleled Data Quality
- Higher Quality Content
- 60% Fewer Hallucinations
Browse by: Latest US Patents, China's latest patents, Technical Efficacy Thesaurus, Application Domain, Technology Topic, Popular Technical Reports.
© 2025 PatSnap. All rights reserved.Legal|Privacy policy|Modern Slavery Act Transparency Statement|Sitemap|About US| Contact US: help@patsnap.com