Para-position aramid fiber paper used for cellular material and preparation method thereof
A technology of para-aramid paper and honeycomb materials, applied in pulp beating methods, synthetic cellulose/non-cellulose material pulp/paper, paper, etc., can solve the problem of affecting the bonding performance of aramid fibers and improve the insulation strength of aramid paper Problems such as running and operating costs, affecting the temperature resistance of paper sheets, etc., achieve the effect of strong innovation, promoting development, and promoting upgrading
- Summary
- Abstract
- Description
- Claims
- Application Information
AI Technical Summary
Problems solved by technology
Method used
Image
Examples
preparation example Construction
[0024] The preparation method of para-aramid paper for honeycomb material of the present invention, as figure 1 As shown, specifically follow the steps below:
[0025] Step 1: the mass molar concentration of aramid chopped fiber is 1.5×10 -3 ~3.0×10 -3 mol / L, sodium dodecylbenzenesulfonate aqueous solution at a temperature of 40~90°C for washing pretreatment, and then washed with water for later use.
[0026] Step 2: Thinning the washed para-aramid chopped fibers with a tank beater to obtain a slurry (A).
[0027] Step 3: The para-aramid pulp fiber is subjected to beating treatment with a trough beater, and the beating degree is controlled at 30-60°SR to make a slurry (B).
[0028] Step 4: The polyimide fiber is decomposed with a trough beater, and the decompression concentration is controlled at 0.5~2% to make a slurry (C).
[0029] Step 5: Add the slurries (A), (B), and (C) into the slurry mixing tank according to the stated weight parts, and add polyethylene oxide as a ...
Embodiment 1
[0031] The mass molar concentration of aramid chopped fiber is 2.3×10 -3 mol / L, sodium dodecylbenzenesulfonate aqueous solution at 60°C for washing and pretreatment, and then rinse with water for later use; use a trough beater to loosen the washed and pretreated para-aramid chopped fibers , made into slurry (A); the para-aramid pulp fiber was beaten by a trough beater, and the beating degree was controlled at 36°SR to make a slurry (B); the polyimide fiber was beaten by a trough The machine is used to decompose, and the decomposed concentration is controlled at 0.5% to make a slurry (C); 30 parts by weight of the slurry (A), (hereinafter referred to as parts), 60 parts of the slurry (B), and 10 parts of (C) are added to the slurry mixing kettle Middle: add polyethylene oxide as a dispersant to mix and disperse the slurry and adjust the slurry concentration to 0.08% of the slurry suspension. Slurry is formed on an inclined wire paper machine, pressed for 1-5 minutes under a pr...
Embodiment 2
[0033] The mass molar concentration of aramid chopped fiber is 1.7×10 -3 mol / L, sodium dodecylbenzene sulfonate aqueous solution at a temperature of 75°C for washing and pretreatment, and then washed with water for later use; use a tank beater to decompose the washed and pretreated para-aramid chopped fibers The slurry (A) is obtained; the para-aramid pulp fiber is beaten with a trough beater, and the beating degree is controlled at 42°SR to make a slurry (B); the polyimide fiber is processed with a trough beater Thawing, the concentration of the thinning is controlled at 1.0%, and the slurry (C) is made; add 40 (parts by weight, hereinafter referred to as parts) of the slurry (A), 40 parts of the slurry (B), and 20 parts of (C) into the slurry mixing kettle: Add polyethylene oxide as a dispersant to mix and disperse the slurry and adjust the slurry concentration to 0.12% of the slurry suspension. The quality of the added dispersant is 1.0% relative to the mass of the para-ara...
PUM
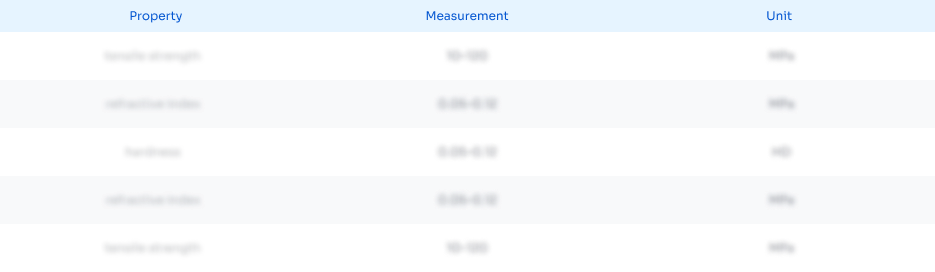
Abstract
Description
Claims
Application Information

- R&D Engineer
- R&D Manager
- IP Professional
- Industry Leading Data Capabilities
- Powerful AI technology
- Patent DNA Extraction
Browse by: Latest US Patents, China's latest patents, Technical Efficacy Thesaurus, Application Domain, Technology Topic, Popular Technical Reports.
© 2024 PatSnap. All rights reserved.Legal|Privacy policy|Modern Slavery Act Transparency Statement|Sitemap|About US| Contact US: help@patsnap.com