Process for manufacturing multielement composition high silica glass fibre fixed-length yarn
A high-silica glass fiber fixed-length and manufacturing process technology, applied in the field of high temperature resistant materials, to achieve the effect of reasonable process design
- Summary
- Abstract
- Description
- Claims
- Application Information
AI Technical Summary
Problems solved by technology
Method used
Image
Examples
Embodiment 1
[0020] see figure 1 , the multi-component high-silica glass fiber staple yarn manufacturing process includes the following steps:
[0021] ①. Using the original glass with sodium-boron-silicon ternary composition as the raw material, the fiber is formed through melting and processing.
[0022] ②. Make yarn bundles by cooling down, twisting, warping and drawing-in in sequence.
[0023] ③. Place the yarn bundle on the creel, control the temperature at 96-98° C., and treat it with steam for 5 hours.
[0024] ④. Put the heat-treated yarn bundle on the creel, then place the creel in the acid leaching tank, inject hydrochloric acid with a concentration of 3.2mol / L into the acid leaching tank for circulation, and perform leaching treatment .
[0025] ⑤. The yarn bundle after the acid leaching treatment is sprayed with water at 25-35° C., and the surface pH value is detected to be 6.7-6.8 to complete the water washing treatment.
[0026] ⑥. Dry at 100-120°C, and then perform post-...
Embodiment 2
[0030] The manufacturing process of multi-component high-silica glass fiber cut-to-length yarn includes the following steps:
[0031] ①. Using the original glass with sodium-boron-silicon ternary composition as the raw material, the fiber is formed through melting and processing.
[0032] ②. Make yarn bundles by cooling down, twisting, warping and drawing-in in sequence.
[0033] ③. Place the yarn bundle on the creel, control the temperature at 97-99° C., and treat it with steam for 5 hours.
[0034] ④. Put the heat-treated yarn bundle on the creel, then place the creel in the acid leaching tank, inject hydrochloric acid with a concentration of 3.2mol / L into the acid leaching tank for circulation, and perform leaching treatment .
[0035] ⑤. The yarn bundle after the acid leaching treatment is sprayed with water at 32-39° C., and the surface pH value is detected to be 6.6-6.7 to complete the water washing treatment.
[0036] ⑥. Dry at 120-140°C, and then perform post-proces...
Embodiment 3
[0039] The manufacturing process of multi-component high-silica glass fiber cut-to-length yarn includes the following steps:
[0040] ①. Using the original glass with sodium-boron-silicon ternary composition as the raw material, the fiber is formed through melting and processing.
[0041] ②. Make yarn bundles by cooling down, twisting, warping and drawing-in in sequence.
[0042] ③. Place the yarn bundle on the creel, control the temperature at 97-98° C., and treat it with steam for 5 hours.
[0043] ④. Put the heat-treated yarn bundle on the creel, then place the creel in the acid leaching tank, inject hydrochloric acid with a concentration of 3.2mol / L into the acid leaching tank for circulation, and perform leaching treatment .
[0044] ⑤. The yarn bundle after the acid leaching treatment is sprayed with water at 35-36° C., and the surface pH value is detected to be 6.5-6.6 to complete the water washing treatment.
[0045] ⑥. Dry at 130-150°C, and then perform post-proces...
PUM
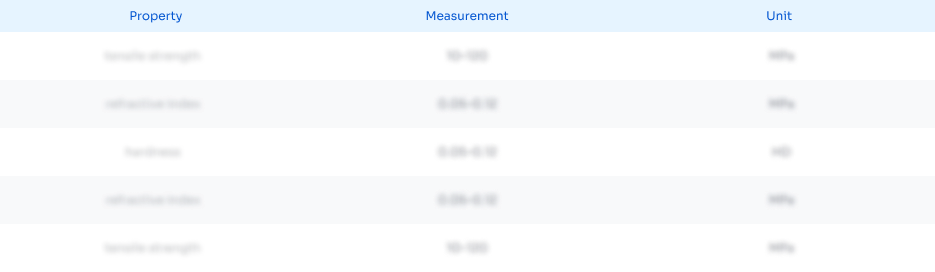
Abstract
Description
Claims
Application Information

- R&D Engineer
- R&D Manager
- IP Professional
- Industry Leading Data Capabilities
- Powerful AI technology
- Patent DNA Extraction
Browse by: Latest US Patents, China's latest patents, Technical Efficacy Thesaurus, Application Domain, Technology Topic, Popular Technical Reports.
© 2024 PatSnap. All rights reserved.Legal|Privacy policy|Modern Slavery Act Transparency Statement|Sitemap|About US| Contact US: help@patsnap.com