Production process of automobile body side impact beam
A production process and anti-side technology, which is applied in the field of automobile parts manufacturing, can solve the problems of easy cracking of sheet metal parts, reduced strength of sheet metal parts, thick wall thickness, etc., and achieve the effect of avoiding easy cracking
- Summary
- Abstract
- Description
- Claims
- Application Information
AI Technical Summary
Problems solved by technology
Method used
Examples
Embodiment
[0023] In this embodiment, the production process of the side impact beam of the vehicle body is as follows:
[0024] Prepare the steel plate, blank it according to the shape of the side impact beam of the vehicle body, and degrease and derust the steel plate that has been blanked; heat the pretreated steel plate, and then press it into shape by a hot stamping machine. and cooling to room temperature; punching and edge trimming are performed on the stamped and cooled steel plate to form a side impact beam for the vehicle body.
[0025] Among them, the stamping process is:
[0026] Put the steel plate on the heater, the heater is located on the feeding mechanism, and the feeding mechanism is located in the closed cavity where the stamping die of the hot stamping machine is located; vacuumize the closed cavity; start the heater, heat the steel plate, and Heating to 690°C at a speed of 9-11°C / s, and then heating to 735-745°C at a speed of 3-5°C / s; the heated steel plate is put i...
PUM
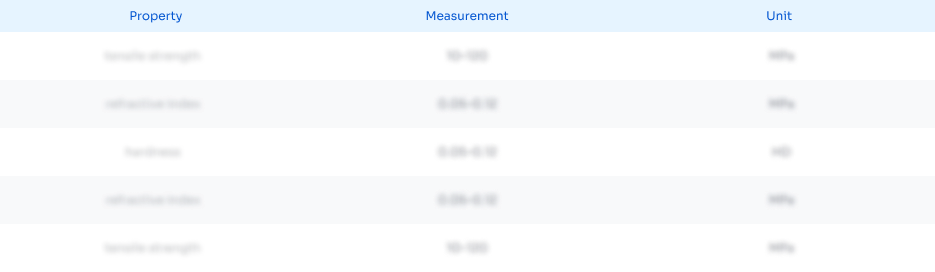
Abstract
Description
Claims
Application Information

- R&D
- Intellectual Property
- Life Sciences
- Materials
- Tech Scout
- Unparalleled Data Quality
- Higher Quality Content
- 60% Fewer Hallucinations
Browse by: Latest US Patents, China's latest patents, Technical Efficacy Thesaurus, Application Domain, Technology Topic, Popular Technical Reports.
© 2025 PatSnap. All rights reserved.Legal|Privacy policy|Modern Slavery Act Transparency Statement|Sitemap|About US| Contact US: help@patsnap.com