Method for preparing silicon nitride by using recovery purification silicon wafer sawdust powder
A technology of silicon nitride and sawdust, which is applied in the field of preparing silicon nitride, can solve the problem of high consumption of additional silicon materials and achieve the effect of reducing costs
- Summary
- Abstract
- Description
- Claims
- Application Information
AI Technical Summary
Problems solved by technology
Method used
Examples
Embodiment 1
[0023] The silicon sawdust powder separated and extracted from the waste mortar discharged from the SiC abrasive mortar wire saw when cutting silicon wafers was used as the raw material. The ICP-AES (plasma-coupled atomic spectrometer) analysis results of the main impurities are listed in Table 1.
[0024] Take 100 grams of the raw material powder, put it in a rotatable corundum tubular resistance furnace, feed ammonia gas, raise the temperature to 600°C, and keep it warm for 1 hour; Keep rotating at a speed of 3 revolutions per minute, and then cool to room temperature with the furnace; then raise the temperature to 1250°C, keep it warm for 2 hours, and then cool to room temperature with the furnace before taking it out of the furnace.
[0025] The product was measured by X-ray powder diffractometer as pure silicon nitride (Si 3 N 4 ), where α-Si 3 N 4 The ratio is 92% v.
[0026] Table 1 ICP-AES analysis results of the main impurities in the silicon sawdust powder raw ma...
Embodiment 2
[0029] The silicon sawdust powder separated and extracted from the waste mortar discharged from the SiC abrasive mortar wire saw when cutting silicon wafers was used as the raw material. The ICP-AES (plasma-coupled atomic spectrometer) analysis results of the main impurities are listed in Table 1.
[0030] Take 100 grams of the raw material powder, place it in a rotatable corundum tubular resistance furnace, feed nitrogen gas, raise the temperature to 800°C, and keep it warm for 3 hours; Keep rotating at a speed of 5 revolutions per minute, and then cool to room temperature with the furnace and take out the furnace; then take the obtained product powder and heat it up to 1350°C in another corundum tube furnace, keep it for 4 hours, and then cool to room temperature with the furnace and then come out of the furnace.
[0031] The product was measured by X-ray powder diffractometer as pure silicon nitride (Si 3 N 4 ), where α-Si 3 N 4 The ratio is 91% v.
Embodiment 3
[0033] The silicon sawdust powder separated and extracted from the waste mortar discharged from the SiC abrasive mortar wire saw when cutting silicon wafers was used as the raw material. The ICP-AES (plasma-coupled atomic spectrometer) analysis results of the main impurities are listed in Table 1.
[0034] Take 100 grams of the raw material powder, put it in a rotatable corundum tubular resistance furnace, pass in nitrogen-hydrogen mixed gas, raise the temperature to 1000°C, and keep it warm for 6 hours; then raise the temperature to 1200°C, keep it warm for 6 hours, The corundum tube keeps rotating at a speed of 30 revolutions per minute, and then cools to room temperature with the furnace; then raises the temperature to 1380°C, keeps it warm for 8 hours, and then cools to room temperature with the furnace and then comes out of the furnace.
[0035] The product was measured by X-ray powder diffractometer as pure silicon nitride (Si 3 N 4 ), where α-Si 3 N 4 The ratio is 95...
PUM
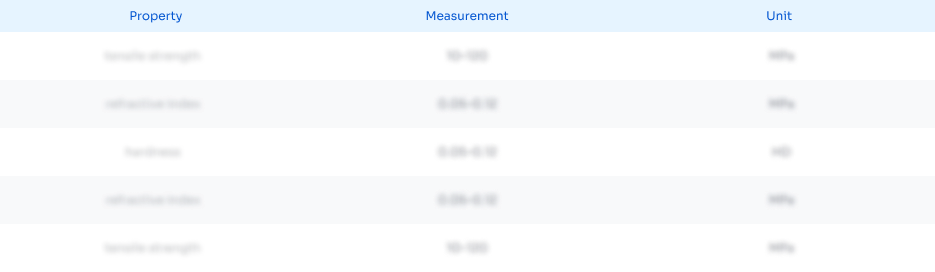
Abstract
Description
Claims
Application Information

- R&D
- Intellectual Property
- Life Sciences
- Materials
- Tech Scout
- Unparalleled Data Quality
- Higher Quality Content
- 60% Fewer Hallucinations
Browse by: Latest US Patents, China's latest patents, Technical Efficacy Thesaurus, Application Domain, Technology Topic, Popular Technical Reports.
© 2025 PatSnap. All rights reserved.Legal|Privacy policy|Modern Slavery Act Transparency Statement|Sitemap|About US| Contact US: help@patsnap.com