Method for producing bronze coated iron powder
A production method and composite powder technology, applied in the direction of coating, etc., can solve the problems of excessive sintering temperature difference, shedding, high temperature adjustment waste, etc., achieve the effect of complete and dense copper layer, avoid pollution and damage, and save intermediate processes
- Summary
- Abstract
- Description
- Claims
- Application Information
AI Technical Summary
Problems solved by technology
Method used
Examples
Embodiment 1
[0027] Copper accounts for 18% (percentage by weight) of the total weight of the composite powder, tin accounts for 1.8% (percentage by weight) of the total weight of the composite powder, and the balance is iron; the specific steps of the method are as follows:
[0028] 1) According to the composition of the bronze-coated iron composite powder, weigh the appropriate amount of copper oxide powder, pure tin powder and iron powder;
[0029] 2), first put the weighed copper oxide powder and pure iron powder in a ball mill or a mixer and mix until the powder color is uniform, then add tin powder and mix evenly;
[0030] 3), move the uniformly mixed powder into the reduction furnace, and carry out the reduction and diffusion under the protection of ammonia decomposition gas or ammonia combustion atmosphere. The reduction and diffusion temperature is 620°C, and the reduction and diffusion treatment time is 1 hour; Cool to below 50°C and release from the oven;
[0031] 4) Crushing a...
Embodiment 2
[0035] Copper accounts for 20% (percentage by weight) of the total weight of the composite powder, tin accounts for 2% (percentage by weight) of the total weight of the composite powder, and the balance is iron; the specific steps of the method are as follows:
[0036] 1) According to the composition of the bronze-coated iron composite powder, weigh the appropriate amount of copper oxide powder, pure tin powder and iron powder;
[0037] 2), first put the weighed copper oxide powder and pure iron powder in a ball mill or a mixer and mix until the powder color is uniform, then add tin powder and mix evenly;
[0038] 3), move the uniformly mixed powder into the reduction furnace, and carry out the reduction and diffusion under the protection of ammonia decomposition gas or ammonia combustion atmosphere. The reduction and diffusion temperature is 730°C, and the reduction and diffusion treatment time is 3 hours; Cool to below 49°C and release from the oven;
[0039] 4) Crushing an...
Embodiment 3
[0043] Copper accounts for 19% (percentage by weight) of the total weight of the composite powder, tin accounts for 2% (percentage by weight) of the total weight of the composite powder, and the balance is iron; the specific steps of the method are as follows:
[0044] 1) According to the composition of the bronze-coated iron composite powder, weigh the appropriate amount of copper oxide powder, pure tin powder and iron powder;
[0045] 2), first put the weighed copper oxide powder and pure iron powder in a ball mill or a mixer and mix until the powder color is uniform, then add tin powder and mix evenly;
[0046] 3), move the uniformly mixed powder into the reduction furnace, and carry out the reduction and diffusion under the protection of ammonia decomposition gas or ammonia combustion atmosphere. The reduction and diffusion temperature is 700 ° C, and the reduction and diffusion treatment time is 2 hours; Cool to below 50°C and release from the oven;
[0047] 4) Crushing ...
PUM
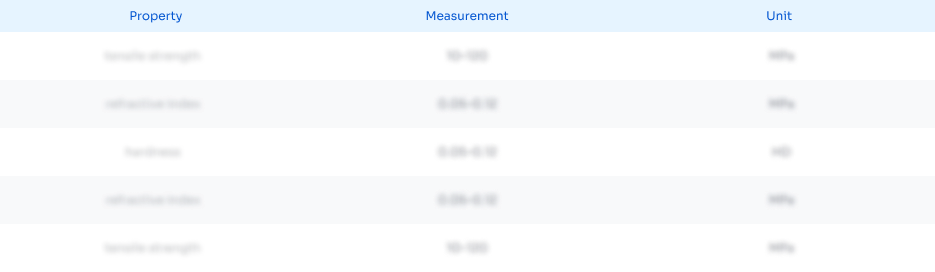
Abstract
Description
Claims
Application Information

- R&D
- Intellectual Property
- Life Sciences
- Materials
- Tech Scout
- Unparalleled Data Quality
- Higher Quality Content
- 60% Fewer Hallucinations
Browse by: Latest US Patents, China's latest patents, Technical Efficacy Thesaurus, Application Domain, Technology Topic, Popular Technical Reports.
© 2025 PatSnap. All rights reserved.Legal|Privacy policy|Modern Slavery Act Transparency Statement|Sitemap|About US| Contact US: help@patsnap.com