Hydraulic forming die and method for manufacturing complex panel component through hydraulic forming die
A hydroforming and mold technology, which is used in the field of molds and the manufacture of complex plate parts, can solve problems such as a lot of time and manpower and material resources, reduced rigidity and strength of parts, and difficulty in meeting quality requirements, and achieves reduction of intermediate processes and thinning rates. Low effect, high material forming limit
- Summary
- Abstract
- Description
- Claims
- Application Information
AI Technical Summary
Problems solved by technology
Method used
Image
Examples
Embodiment 1
[0046] A kind of hydroforming mold, comprises upper mold 1 and lower mold 2, described lower mold is mold, upper mold is empty mold, described lower mold comprises lower mold body 21 and the lower mold cavity 22 that opens in the middle part of lower mold body, The lower mold cavity is a concave mold corresponding to the shape of the plate-shaped part to be produced (the inner cavity of the lower mold is designed to be the shape of the part to be produced), and the bottom of the lower mold cavity is provided with an air vent 25, surrounding the lower mold cavity The lower mold body has a lower locking screw hole 23 and a lower positioning pin hole 24; the upper mold 1 includes an upper mold body 11 and an upper mold cavity 12 opened in the middle of the upper mold body, and the upper mold cavity is compatible with the upper mold body. The cavity of the lower mold cavity is opposite to the mouth of the cavity, and an installation groove 15 for installing a sealing ring is provid...
Embodiment 2
[0049] A method of manufacturing complex sheet metal parts using a hydroforming die, comprising the steps of:
[0050] S1: Simulation analysis, analyzing the maximum deformation of the plate parts and the following production parameters: the pressure of the compressed liquid during forming, the lubrication coefficient between the plate and the upper die and the plate and the lower die, the forming time of the plate, springback The rate is based on the dwell time and liquid loading path corresponding to the rebound rate;
[0051] The loading path includes:
[0052] (1) Linear loading, that is, loading with equal slope of hydraulic pressure;
[0053] (2) Constant loading, that is, the loading parameter rating;
[0054] (3) Step loading, that is, the hydraulic pressure is suddenly loaded with a certain value;
[0055] S2: Open the upper and lower molds, install the sealing ring in the installation groove, place the plate with a size slightly smaller than the cross-section of the...
PUM
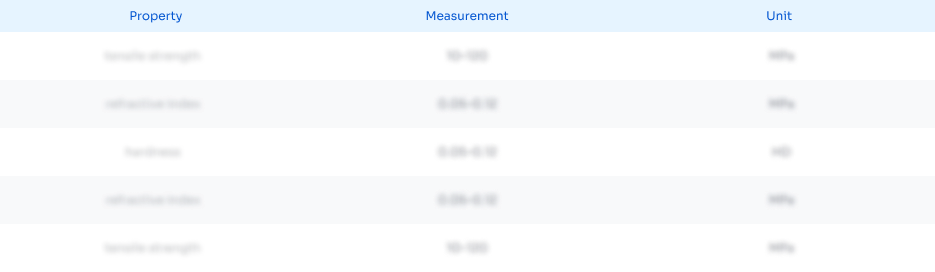
Abstract
Description
Claims
Application Information

- R&D
- Intellectual Property
- Life Sciences
- Materials
- Tech Scout
- Unparalleled Data Quality
- Higher Quality Content
- 60% Fewer Hallucinations
Browse by: Latest US Patents, China's latest patents, Technical Efficacy Thesaurus, Application Domain, Technology Topic, Popular Technical Reports.
© 2025 PatSnap. All rights reserved.Legal|Privacy policy|Modern Slavery Act Transparency Statement|Sitemap|About US| Contact US: help@patsnap.com