Super hydrophobic-supper lipophilic polymer porous film, preparation method and application thereof
A porous membrane and super lipophilic technology, applied in chemical instruments and methods, membrane technology, semi-permeable membrane separation, etc., can solve the problems of inability to separate emulsified oil with small particle size, poor separation membrane strength, etc., and achieve the preparation process Simple operation, efficient separation, and controllable thickness
- Summary
- Abstract
- Description
- Claims
- Application Information
AI Technical Summary
Problems solved by technology
Method used
Image
Examples
preparation example Construction
[0025] The preparation method of the superhydrophobic-superoleophilic polymer porous membrane is as follows: mixing small molecular substances and polymer material solutions in a set ratio, spreading the resulting mixed solution on the surface of the substrate, and then forming a film through a wet phase inversion process .
[0026] Furthermore, it is obvious that based on the foregoing content of this specification, those skilled in the art can easily imagine that by controlling the type and concentration (or ratio) of polymer materials and small molecule additives in the mixed solution, the amount and extension of the mixed solution Area, and then prepare membranes with different strengths, thicknesses and areas to meet the needs of practical applications.
[0027] For example, as a preferred embodiment of the present invention, the concentration of the polymer material in the mixed solution may be 0.05-40wt%, and the small-molecule additive may be 0.01-70wt%.
[0028] Pref...
Embodiment 1
[0038] Weigh polyvinylidene fluoride (PVDF) and dissolve it in N-methylpyrrolidone (NMP) to prepare 1ml of 0.1g / ml solution; measure 40ul of NaOH aqueous solution (concentration: 1.5wt%) and slowly add it under the condition of magnetic stirring Add the above PVDF solution and stir until homogeneous. After scraping the above mixed solution on the surface of the pre-cleaned glass substrate, transfer it to a water bath (water bath temperature: 25±1°C) for curing. Then the membrane is taken out from the water bath and dried at room temperature to obtain the finished superhydrophobic-superoleophilic polymer porous membrane, the surface structure of which can be found in figure 2 , while its contact angle for aqueous systems is 158° (see figure 1 ).
Embodiment 2
[0040] Weigh polyvinylidene fluoride (PVDF) and dissolve it in N-methylpyrrolidone (NMP) to prepare 1ml of 0.05g / ml solution; measure 20ul of pure water, slowly add it to the above PVDF solution under magnetic stirring conditions, and stir to uniform. After casting the above mixed solution on the surface of the pre-cleaned glass substrate to form a film, transfer it to a water bath (water bath temperature: 15±1°C) for curing. Then the membrane is taken out from the water bath and dried at room temperature to obtain the finished superhydrophobic-superoleophilic polymer porous membrane.
PUM
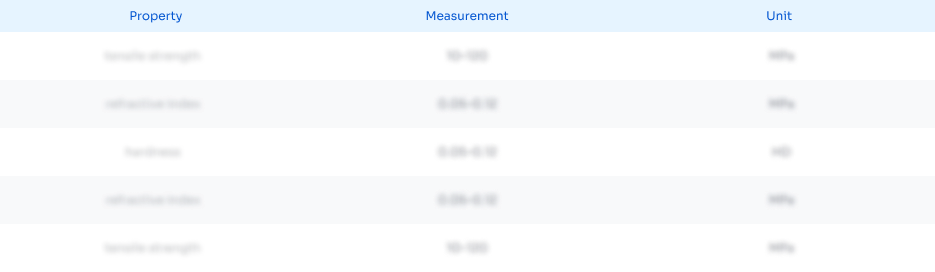
Abstract
Description
Claims
Application Information

- R&D
- Intellectual Property
- Life Sciences
- Materials
- Tech Scout
- Unparalleled Data Quality
- Higher Quality Content
- 60% Fewer Hallucinations
Browse by: Latest US Patents, China's latest patents, Technical Efficacy Thesaurus, Application Domain, Technology Topic, Popular Technical Reports.
© 2025 PatSnap. All rights reserved.Legal|Privacy policy|Modern Slavery Act Transparency Statement|Sitemap|About US| Contact US: help@patsnap.com