Power conversion device
A technology of power conversion device and power converter, which is applied in the direction of controlling electromechanical transmission device, output power conversion device, electronic commutation motor control, etc., can solve the problems of smoothing capacitor damage, motor current ripple, pulsation, etc., and achieve improved stability sex, reduce the effect of pulsation
- Summary
- Abstract
- Description
- Claims
- Application Information
AI Technical Summary
Problems solved by technology
Method used
Image
Examples
Embodiment approach 1
[0057] figure 1 The first embodiment of the present invention is shown. in figure 1 Here, the AC voltage supplied by the three-phase AC power supply 101 is transformed by the transformer 102, rectified by the diode parts 103U, 103V, and 103W, and smoothed by the smoothing capacitors 104U, 104V, and 104W to obtain the DC voltage.
[0058] The 5-stage power converter 105U obtained by connecting single-phase 3-stage power converters 201A and 201B in series, the 5-stage power converter 105V obtained by connecting single-phase 3-stage power converters 202A and 202B in series, and the single-phase 3-stage power converter 105V The five-stage power converter 105W obtained by connecting the power converters 203A and 203B in series converts the DC voltage into AC of arbitrary frequency and phase, and supplies it to the AC motor 106 to perform variable speed control of the AC motor.
[0059] The output current detector 107 detects the U-phase, V-phase, and W-phase output currents in the AC ...
Embodiment approach 2
[0086] Next, regarding the second embodiment of the present invention, the differences from the first embodiment will be described. In Embodiment 1, the number of pulses is set to a multiple of 3, but as Figure 14 As shown, all integer pulses added with integers other than multiples of 3 can be used.
[0087] When the number of pulses is set as in the present embodiment, when the number of pulses is not a multiple of 3, the phase voltage command value V of the V phase and W phase V * , V W * With the positive side triangular wave carrier C u , The negative side triangle wave carrier C d The comparison of carrier waveform is as Figure 15 Shown, T VI Period and t VII Output voltage during the period V V , And, T WI Period and t WII Output voltage during the period V W It is asymmetrical with respect to the axis 401. So like Figure 16 As shown, by making the positive side triangular wave carrier C u , The negative side triangle wave carrier C d The phase shift of +120°, or -12...
Embodiment approach 3
[0092] Next, regarding the third embodiment of the present invention, the differences from the first and second embodiments will be described. In the first embodiment, for the strobe signal G U_A , G U_B , Set two positive-side triangular wave carriers C of the same waveform with different offset values u , The negative side triangle wave carrier C d , Through the phase voltage command value V U * , -V U * Compare to output, but it can also be as Figure 17 As shown, a triangular wave carrier is set, the phase voltage command values with different offset values are made, compared with the carrier waveform, and the strobe signal G is output U_A , G U_B . At this time, the offset value is the distance between the peak and the trough of the triangular wave carrier. Figure 17 Set to 1. By changing the phase voltage command value V U * , -V U * Such as Figure 17 As shown moves upward, the distance between the peak and the trough of the triangular wave carrier is 1, so that the ...
PUM
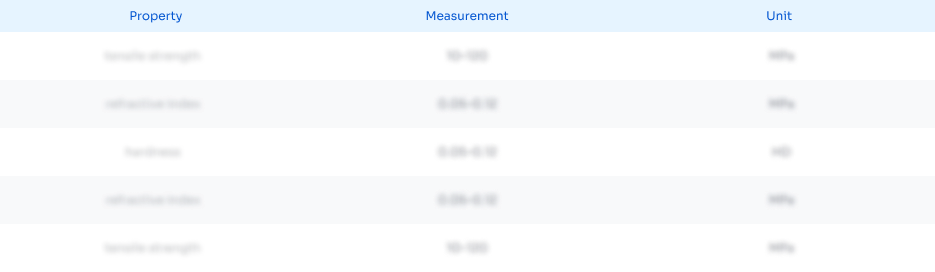
Abstract
Description
Claims
Application Information

- Generate Ideas
- Intellectual Property
- Life Sciences
- Materials
- Tech Scout
- Unparalleled Data Quality
- Higher Quality Content
- 60% Fewer Hallucinations
Browse by: Latest US Patents, China's latest patents, Technical Efficacy Thesaurus, Application Domain, Technology Topic, Popular Technical Reports.
© 2025 PatSnap. All rights reserved.Legal|Privacy policy|Modern Slavery Act Transparency Statement|Sitemap|About US| Contact US: help@patsnap.com