Glass-fiber-reinforced hydrolysis-resistant polyester material and preparation method thereof
A technology of glass fiber and polyester materials, which is applied in the field of modified polyester materials and their preparation, can solve the problems of not being able to know the hydrolysis resistance performance, and the method of hydrolysis resistance performance has not been improved, etc., and achieve excellent processing performance, low cost, good fluidity
- Summary
- Abstract
- Description
- Claims
- Application Information
AI Technical Summary
Problems solved by technology
Method used
Image
Examples
Embodiment 1
[0042] Embodiment 1 Preparation of polyester material of the present invention (1)
[0043] (1) Weigh the following raw materials by weight percentage: PBT 60%, glass fiber ECS13-4.5-534A 30%, compatibilizer AX8900 3.8%, carbodiimide 0.5%, epoxy resin 5%, antioxidant 1098 0.2 %, antioxidant 168 0.2%, lubricant MB-4 0.3%;
[0044] (2) Bake the PBT weighed in step 1) at 110°C for 8 hours;
[0045] (3) Put all raw materials into a high-efficiency mixer and mix for 8 minutes before discharging;
[0046] (4) Put the mixed raw materials in step 3 into a twin-screw extruder to melt, knead, extrude and water-cool, then dry, cut into pellets, and pack. The speed of the screw machine is 260 rpm. The temperature of each section of the barrel of the twin-screw extruder is 235-255°C.
Embodiment 2
[0047] Embodiment 2 Preparation of polyester material of the present invention (2)
[0048](1) Weigh the following raw materials by weight percentage: PBT 40%, PET 20%, glass fiber ECS13-4.5-534A 30%, compatibilizer AX8900 3.8%, carbodiimide 0.5%, isocyanate 5%, antioxidant 1098 0.2%, antioxidant 168 0.2%, lubricant TAF 0.3%;
[0049] (2) Bake the PBT and PET weighed in step 1) at 110°C for 8 hours;
[0050] (3) Put all raw materials into a high-efficiency mixer and mix for 5 minutes before discharging;
[0051] (4) Put the mixed raw materials in step 3 into a twin-screw extruder to melt, knead, extrude and water-cool, then dry, cut into pellets, and package. The screw machine rotates at 500 rpm. The temperature of each section of the barrel of the twin-screw extruder is 235-255°C.
Embodiment 3
[0052] Example 3 Preparation of polyester material of the present invention (3)
[0053] (1) Weigh the following raw materials by weight percentage: PET 70%, glass fiber ECS13-4.5-534A 15%, compatibilizer PTW 10%, cyclic anhydride 2%, oxazole derivative 2.5%, antioxidant 1098 0.1% , antioxidant 168 0.1%, lubricant TAF 0.2%, lubricant MB-4 0.1%;
[0054] (2) Dry the PET weighed in step 1) at 110°C for 7.5 hours;
[0055] (3) Put all raw materials into a high-efficiency mixer and mix for 10 minutes before discharging;
[0056] (4) Put the mixed raw materials in step 3 into a twin-screw extruder to melt, knead, extrude and water-cool, then dry, cut into pellets, and package. The screw machine rotates at 180 rpm. The temperature of each section of the barrel of the twin-screw extruder is 235-255°C.
PUM
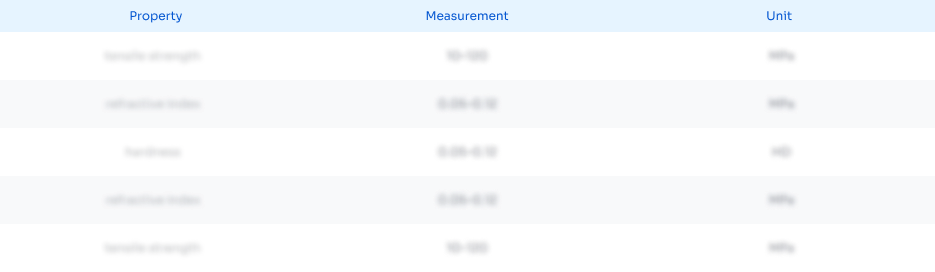
Abstract
Description
Claims
Application Information

- R&D
- Intellectual Property
- Life Sciences
- Materials
- Tech Scout
- Unparalleled Data Quality
- Higher Quality Content
- 60% Fewer Hallucinations
Browse by: Latest US Patents, China's latest patents, Technical Efficacy Thesaurus, Application Domain, Technology Topic, Popular Technical Reports.
© 2025 PatSnap. All rights reserved.Legal|Privacy policy|Modern Slavery Act Transparency Statement|Sitemap|About US| Contact US: help@patsnap.com