Carbon nano tube/thermosetting resin composite material and preparation method thereof
A resin composite material, carbon nanotube technology, applied in the direction of fibrous filler, dyed organosilicon compound treatment, etc., can solve the problems of poor performance of modified resin, poor preparation process of modified resin, etc., to achieve good flame retardancy, The effect of improving toughness and flame retardancy
- Summary
- Abstract
- Description
- Claims
- Application Information
AI Technical Summary
Problems solved by technology
Method used
Image
Examples
Embodiment 1
[0039] 1. Synthesis of hyperbranched polysiloxane containing phosphaphenanthrene structure and amino groups
[0040] Under the conditions of anhydrous and nitrogen protection, 23.6g 3-glycidyl etheroxypropyltrimethoxysilane and 21.6g 9,10-dihydro-9-oxa-10-phosphaphenanthrene-10-oxide After mixing evenly, add 0.45g of catalyst triphenylphosphine, add 100g of n-propanol, heat up to 95°C and keep condensing and refluxing to continue the reaction for 6 hours; after the reaction is completed, remove the solvent by distillation under reduced pressure, remove the catalyst by filtration, and carry out vacuum drying to obtain Transparent trialkoxysilane containing phosphaphenanthrene structure and hydroxyl, see the attached figure 1 .
[0041] Take all the above-mentioned trialkoxysilanes containing phosphaphenanthrene structures and hydroxyl groups, 1.8g 3-aminopropyltrimethoxysilane and 2.2g distilled water, mix evenly, heat to 50°C for 4 hours, and distill under reduced pressure to...
Embodiment 2
[0059] 1. Synthesis of Phosphophenanthrene Structure and Amino Hyperbranched Polysiloxane
[0060]Under the conditions of anhydrous and nitrogen protection, 24.6g 2-(3,4-epoxycyclohexyl)ethyltrimethoxysilane and 21.6g 9,10-dihydro-9-oxa-10-phosphorus After the heterophenanthrene-10-oxide is mixed evenly, add 1.4g of catalyst triphenylphosphine, add 100g of methanol, raise the temperature to 100°C and keep condensing and refluxing to continue the reaction for 10 hours; The catalyst was removed by filtration to obtain a transparent trialkoxysilane containing a phosphaphenanthrene structure and a hydroxyl group.
[0061] Take all the above-mentioned trialkoxysilanes containing phosphaphenanthrene structures and hydroxyl groups, 2.2g 3-aminopropyltrimethoxysilane and 2.2g distilled water, mix evenly, heat to 60°C for 7 hours, and distill under reduced pressure to obtain crude product;
[0062] After purification, filtration, vacuum distillation and vacuum drying of the crude pro...
Embodiment 3
[0068] 1. Synthesis of phosphophenanthrene structure and amino hyperbranched polysiloxane
[0069] Under the conditions of anhydrous and nitrogen protection, 24.6g 2-(3,4-epoxycyclohexanealkyl)ethyltrimethoxysilane and 21.6g 9,10-dihydro-9-oxa-10- After the phosphaphenanthrene-10-oxide is mixed evenly, add 1.3g of catalyst triphenylphosphine, add 100g of ethanol, raise the temperature to 97°C and keep condensing and refluxing to continue the reaction for 8 hours; The catalyst is removed by filtration to obtain a transparent trialkoxysilane containing a phosphaphenanthrene structure and a hydroxyl group.
[0070] Take all the above-mentioned trialkoxysilanes containing phosphaphenanthrene structures and hydroxyl groups, 17.9g 3-aminopropyltrimethoxysilane and 2.2g distilled water, mix evenly, heat to 55°C for 7 hours, and distill under reduced pressure to obtain crude product;
[0071] After purification, filtration, vacuum distillation and vacuum drying of the crude product,...
PUM
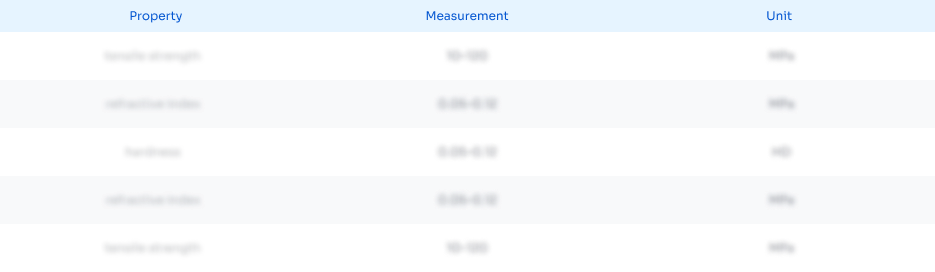
Abstract
Description
Claims
Application Information

- R&D
- Intellectual Property
- Life Sciences
- Materials
- Tech Scout
- Unparalleled Data Quality
- Higher Quality Content
- 60% Fewer Hallucinations
Browse by: Latest US Patents, China's latest patents, Technical Efficacy Thesaurus, Application Domain, Technology Topic, Popular Technical Reports.
© 2025 PatSnap. All rights reserved.Legal|Privacy policy|Modern Slavery Act Transparency Statement|Sitemap|About US| Contact US: help@patsnap.com