Microporous composite brake pad for high-speed railway and manufacturing method of microporous composite brake pad
A technology for high-speed railways and manufacturing methods, applied to friction linings, mechanical equipment, etc., can solve the problems of brake disc thermal cracks, long production cycle, expensive price, etc., and achieve the reduction of friction surface temperature, short production cycle, and heat dissipation effect Good results
- Summary
- Abstract
- Description
- Claims
- Application Information
AI Technical Summary
Problems solved by technology
Method used
Examples
Embodiment 1
[0034] A method for manufacturing a microporous composite brake pad for high-speed railways, comprising the following steps:
[0035] (1) Preparation of raw materials:
[0036] Component Weight percent
[0037] Polyimide modified resin 10%
[0038] Friction modifier 12%
[0039] Precipitated barium sulfate 20%
[0040] Graphite 25%
[0041] Aramid pulp 1%
[0042] Chopped carbon fiber 20%
[0044] Among them, the friction modifier is vulcanizing agent PDM.
[0045] (2) Preparation:
[0046] The above-mentioned raw materials are added to the high-speed rake mixer in proportion and mixed step by step. The mixing time is 3 minutes. The material is reacted in the molding mold with a pressure of 250kg / cm2 for 400 seconds at 50°C. The formed brake disc is then sintered at high temperature. The sintering temperature is 160° C., and the sintering time is 16 hours to obtain a microporous high-porosity brake sheet.
Embodiment 2
[0048] A method for manufacturing a microporous composite brake pad for high-speed railways, comprising the following steps:
[0049] (1) Preparation of raw materials:
[0050] Component Weight percent
[0051] Silicone modified resin 13%
[0052] Friction modifier 15%
[0053] Precipitated Barium Sulfate 25%
[0054] Graphite 27%
[0055] Aramid pulp 1.5%
[0056] Chopped carbon fiber 15%
[0058] The friction modifier is organic bentonite.
[0059] (2) Preparation:
[0060] The above-mentioned raw materials are added to the high-speed rake mixer in proportion and mixed step by step. The mixing time is 4 minutes. The material is reacted in the molding mold at a pressure of 270kg / cm2 for 400 seconds at 80°C. The formed brake disc is then sintered at high temperature. The sintering temperature is 200° C., and the sintering time is 16 hours, and the microporous high-porosity brake sheet can be obtained.
Embodiment 3
[0062] A method for manufacturing a microporous composite brake pad for high-speed railways, comprising the following steps:
[0063] (1) Preparation of raw materials:
[0064] Component Weight percent
[0065] Cashew shell liquid modified resin 15%
[0066] Friction modifier 8%
[0067] Precipitated barium sulfate 30%
[0068] Graphite 30%
[0069] Aramid pulp 2%
[0070] Chopped Carbon Fiber 10%
[0072] Wherein the friction modifier is kaolin.
[0073] (2) Preparation:
[0074] The above-mentioned raw materials are added to the high-speed rake mixer in proportion and mixed step by step. The mixing time is 5 minutes. The material is reacted in the molding mold at a pressure of 350kg / cm2 for 400 seconds at room temperature to 100°C. The formed brake disc is then sintered at high temperature. The sintering temperature is 160° C., and the sintering time is 12 hours, and the microporous high-porosity brake sheet can be obtained.
PUM
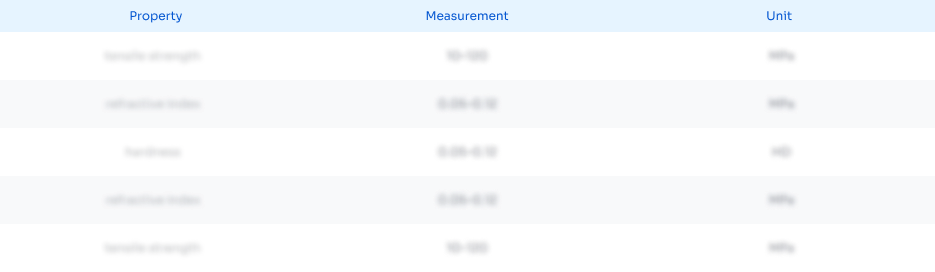
Abstract
Description
Claims
Application Information

- R&D
- Intellectual Property
- Life Sciences
- Materials
- Tech Scout
- Unparalleled Data Quality
- Higher Quality Content
- 60% Fewer Hallucinations
Browse by: Latest US Patents, China's latest patents, Technical Efficacy Thesaurus, Application Domain, Technology Topic, Popular Technical Reports.
© 2025 PatSnap. All rights reserved.Legal|Privacy policy|Modern Slavery Act Transparency Statement|Sitemap|About US| Contact US: help@patsnap.com