Preparation method of beta crystalline form polypropylene resin
A technology of polypropylene resin and β-crystal form, which is applied in the field of preparation of β-crystal form polypropylene resin, can solve the problems of uneven dispersion, difficult dispersion of nucleating agent, large amount of nucleating agent added, etc., and achieve tensile yield strength Improvement, impact resistance improvement, heat resistance improvement effect
- Summary
- Abstract
- Description
- Claims
- Application Information
AI Technical Summary
Problems solved by technology
Method used
Image
Examples
Embodiment 1~12
[0045] 1) The temperature of the 450ml slurry polymerization reactor is raised to a temperature of 50-90° C. and vacuum-dried, and the air and traces of water in the slurry polymerization reactor are replaced with nitrogen with a purity of 99.99%, and the temperature is lowered to Polymerization temperature;
[0046] 2) feed propylene gas into the slurry polymerization reactor of step 1), make the pressure in the slurry polymerization reactor rise to normal pressure, then use heptane or hexane to dry the The polypropylene β crystal nucleating agent is washed into the slurry polymerization reactor of step 1); then the triethylaluminum cocatalyst, the diphenyldimethoxysilane external electron donor and the MgCl 2 / ID / TiCl 4 The supported Ziegler-Natta catalyst is added into the slurry polymerization reactor and stirred;
[0047] Wherein, the adding amount of described dry polypropylene beta crystal form nucleating agent is shown in Table 1, triethylaluminum cocatalyst: MgCl 2...
Embodiment 13~19
[0056] The experiments of Examples 13-19 were carried out according to the test formulation in Table 3.
[0057] 1) Before the polymerization starts, purge the bulk polymerization reactor with high-purity nitrogen with a purity of 99.99%, and replace the air and traces of water in the bulk polymerization reactor with high-purity nitrogen to ensure that the bulk polymerization reactor is removed. air and traces of water;
[0058] 2) Based on the content of the beta crystal form nucleating agent in the polypropylene resin, add hydrogen and liquid propylene to the bulk polymerization reactor of step 1), wherein the liquid propylene is in the range of 0.7kg to 2.8kg, and the hydrogen is in the range of 100 Within the range of ~376mmol, stir at a speed of 300rpm / min;
[0059] 3) Add 314mg~3010mg β-crystal nucleating agent, 35.36~70.72mmol triethylaluminum cocatalyst, 0.884mmol~1.768mmol diphenyldimethoxysilane (external electron donor) to the body of step 2) In the feeder on the ...
Embodiment 20~25
[0065] The steps of bulk polymerization described in table 5 are:
[0066] 1) Before the polymerization starts, purge the bulk polymerization reactor with high-purity nitrogen with a purity of 99.99%, and replace the air and traces of water in the bulk polymerization reactor with high-purity nitrogen to ensure that the bulk polymerization reactor is removed. air and traces of water;
[0067] 2) The experiments of Examples 20 to 25 in Table 5 are based on the content of the β crystal nucleating agent in the polypropylene resin, and 0.7 kg of liquid propylene and 100 mmol of hydrogen are added to the bulk polymerization reactor of step 1), 790mg β crystal nucleating agent, 0.884mmol diphenyldimethoxysilane external electron donor, 35.36mmol triethylaluminum cocatalyst are joined in the feeder on the bulk polymerization reactor top of step 1); Use 0.05kg Liquid propylene flushes the external β crystal nucleating agent, diphenyldimethoxysilane external electron donor, and triethy...
PUM
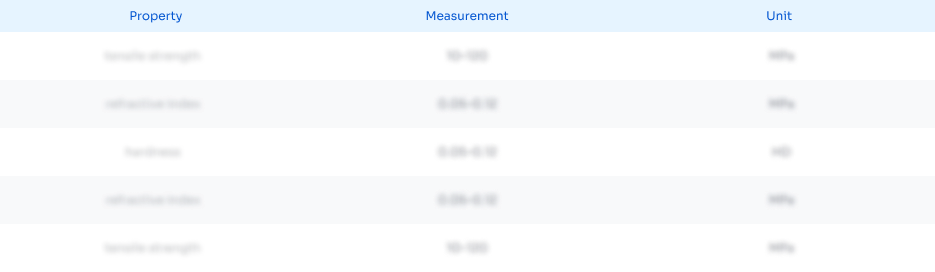
Abstract
Description
Claims
Application Information

- Generate Ideas
- Intellectual Property
- Life Sciences
- Materials
- Tech Scout
- Unparalleled Data Quality
- Higher Quality Content
- 60% Fewer Hallucinations
Browse by: Latest US Patents, China's latest patents, Technical Efficacy Thesaurus, Application Domain, Technology Topic, Popular Technical Reports.
© 2025 PatSnap. All rights reserved.Legal|Privacy policy|Modern Slavery Act Transparency Statement|Sitemap|About US| Contact US: help@patsnap.com