Preparation method of core-shell talc powder-polypropylene composite material
A composite material and talc technology, applied in the polymer field, can solve the problems of uneven surface coating and large amount of coupling agent, and achieve the effect of improving surface affinity and improving performance
- Summary
- Abstract
- Description
- Claims
- Application Information
AI Technical Summary
Problems solved by technology
Method used
Image
Examples
Embodiment 1
[0021] (1), 200 g of talc powder passed through a 600 mesh sieve and 0.2 g of coupling agent vinyl tris (β-methoxyethoxy) silane were blended for 3 minutes to obtain talcum powder activated by coupling agent;
[0022] (2) Add 40 g of the above-mentioned active talcum powder under stirring in 600 g of toluene, and maintain for 10 min to form a stable suspension; add 0.06 g of N-IV type initiator, pass propylene gas until the propylene is dissolved and balanced (P=100kPa), the total pressure of the system Maintained at 140kPa, the temperature was 30°C, and the polymerization reaction was carried out for 1h under stirring. The product was filtered, washed several times with alcohol, dried under vacuum at 40°C, and weighed; the core-shell talc-polypropylene composite material was obtained.
[0023] The composite material was filled with PP, and samples were prepared by extrusion and injection molding. The test results are shown in Table 1.
Embodiment 2
[0025] (1) 200 g of 6000-mesh talcum powder was blended with 4 g of coupling agent vinyl tris(β-methoxyethoxy)silane for 10 minutes to obtain talcum powder activated by coupling agent;
[0026] (2) Add all the above-mentioned active talc powder into 1200g of toluene under stirring, and maintain it for 10 minutes to form a stable suspension. Add 1.2g N-IV type initiator, blow propylene gas until the propylene dissolves equilibrium (P=100kPa), maintain the total pressure of the system at 140kPa, the temperature is 60°C, and polymerize for 3h under stirring. The product was filtered, washed several times with alcohol, dried under vacuum at 70°C, and weighed.
[0027] The composite material was filled with PP, and samples were prepared by extrusion and injection molding. The test results are shown in Table 1.
Embodiment 3
[0029] (1) Blend 200 g of 3000-mesh talcum powder with 2 g of coupling agent vinyl tris(β-methoxyethoxy)silane for 5 minutes to obtain talcum powder activated by coupling agent;
[0030] (2) Add 100 g of the above-mentioned active talc powder into 600 g of toluene under stirring, and maintain for 10 min to form a stable suspension. Add 0.3g N-IV type initiator, pass propylene gas until the propylene dissolves equilibrium (P=100kPa), maintain the total pressure of the system at 140kPa, the temperature is 60°C, and polymerize for 2h under stirring. The product was filtered, washed several times with alcohol, dried under vacuum at 50°C, and weighed. The composite material was filled with PP, and samples were prepared by extrusion and injection molding. The test results are shown in Table 1.
[0031] Table 1
[0032]
[0033] Under a certain filling amount, the prepared core-shell talc powder-polypropylene composite can effectively improve the rigidity and dimensional stabili...
PUM
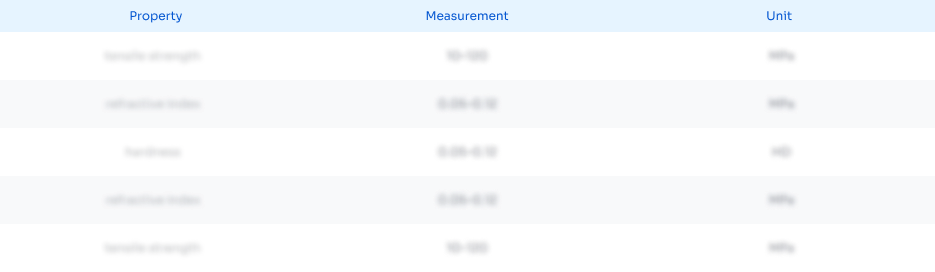
Abstract
Description
Claims
Application Information

- R&D
- Intellectual Property
- Life Sciences
- Materials
- Tech Scout
- Unparalleled Data Quality
- Higher Quality Content
- 60% Fewer Hallucinations
Browse by: Latest US Patents, China's latest patents, Technical Efficacy Thesaurus, Application Domain, Technology Topic, Popular Technical Reports.
© 2025 PatSnap. All rights reserved.Legal|Privacy policy|Modern Slavery Act Transparency Statement|Sitemap|About US| Contact US: help@patsnap.com