Transformation method for mixed rare earth concentrate and concentrated sulfuric acid low-temperature roasted ore
A mixed rare earth and low-temperature roasting technology, which is applied in the direction of improving process efficiency, can solve the problems of many transformation steps, high consumption of chemical reagents, and restrictions on the promotion of low-temperature roasting process of concentrated sulfuric acid.
- Summary
- Abstract
- Description
- Claims
- Application Information
AI Technical Summary
Problems solved by technology
Method used
Image
Examples
Embodiment 1
[0083] The roasted ore products produced by low-temperature roasting are processed separately by using the thick slurry transformation method and the current traditional water leaching, double salt precipitation, alkali conversion and acid-dissolution methods.
[0084] A. Primary grinding of roasted ore: After cooling the low-temperature roasted ore product to 98°C, put it into the storage bin 1, and feed it to the ball mill 3 through the vibrating feeder 2. The ball mill 3 grinds the roasted ore to less than 1mm, and the ball mill 3 is equipped with ventilation. Dust removal system, the ventilation and dust removal system keeps the primary grinder from the feed port to the discharge port to maintain the forward airflow, and collects the dust generated by the grinding into the bag filter 5, and combines the recovered dust with the fine materials obtained by grinding, and the ball mill 3 grinds the obtained fine materials Through the material belt conveyor 4, it is continuously ...
Embodiment 2
[0090] Except following steps, the step of this embodiment is identical with thick slurry transformation embodiment 1:
[0091] The residence time of the secondary grinding is 60 minutes, and the weight ratio of ammonium bicarbonate, roasted ore fines and water used is 1: 2.2: 9.1, that is, based on the treatment of 1000g dry ore, the amount of ammonium bicarbonate added is 942g, adding 8.2 kg of water for washing; 820 g of nitric acid was used in the acid dissolution step, and the pH was adjusted to 3; the pH value was adjusted to 5 in the purification step, and 20 g of barium chloride was added. Obtain 1.5 liters of rare earth nitric acid solutions through the above steps, obtain acid-dissolved slag 600g, contain ammonium sulfate 120g / liter, ammonium hydrogen phosphate and ammonium dihydrogen phosphate (in ammonium phosphate) 10 g / liter of waste water 9 liters.
Embodiment 3
[0093] Except following steps, the step of this embodiment is identical with thick slurry transformation embodiment 1:
[0094] Directly carry out the grinding and thickening conversion operation, the grinding and thickening conversion step lasts for 120 minutes, and the weight ratio of ammonium bicarbonate, roasted ore fine material and water used is 1: 2.2: 9.1, that is, based on the treatment of 1000g of dry ore, The amount of ammonium bicarbonate added is 942g, and 8.5kg of washing water is added; the acid dissolution step uses 820g of nitric acid, wherein the pH is adjusted to 1.5; the purification step is adjusted to a pH value of 5, and 20g of barium chloride is added. Obtain 1.3 liters of rare earth nitric acid solution through the above steps, obtain acid-dissolved slag 620g, contain ammonium sulfate 126g / liter, ammonium hydrogen phosphate and ammonium dihydrogen phosphate (calculated as ammonium phosphate) 11 grams / liter of waste water 8.5 liters.
[0095] 3. The cur...
PUM
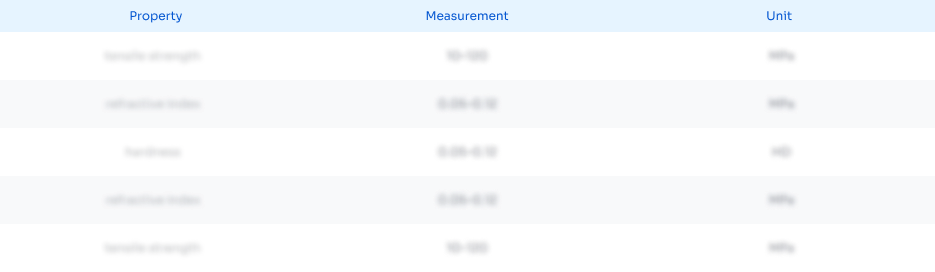
Abstract
Description
Claims
Application Information

- Generate Ideas
- Intellectual Property
- Life Sciences
- Materials
- Tech Scout
- Unparalleled Data Quality
- Higher Quality Content
- 60% Fewer Hallucinations
Browse by: Latest US Patents, China's latest patents, Technical Efficacy Thesaurus, Application Domain, Technology Topic, Popular Technical Reports.
© 2025 PatSnap. All rights reserved.Legal|Privacy policy|Modern Slavery Act Transparency Statement|Sitemap|About US| Contact US: help@patsnap.com