Fire coal desulfurization and denitrification decoking additive and preparation process thereof
A technology of desulfurization, denitrification and additives, which is applied in the field of clean coal, can solve the problems of poor desulfurization effect and low desulfurization rate, and achieve the effects of improving the small combustion environment, reducing the blackness of exhaust smoke, and reducing emissions
- Summary
- Abstract
- Description
- Claims
- Application Information
AI Technical Summary
Problems solved by technology
Method used
Examples
Embodiment 1
[0016] 1) Preparation of pulverized coal additives: 20% sodium carbonate, 10% magnesium oxide, 13% silica, 6% zinc oxide, 8% manganese dioxide, 7% barium oxide and 3% copper oxide was sequentially added and stirred for 20 minutes, then 25% activated calcium oxide and 8% ammonium bicarbonate were added and stirred for 10 minutes, and mixed uniformly to obtain a coal powder additive;
[0017] 2) Preparation of catalytic activator: stir 20% of activated calcium oxide, 30% of activated alumina, and 20% of light burnt magnesium for 15 minutes, and then add 20% of activated carbon and 10% of calcium ammonium nitrate to stir. The catalyst activator is uniformly obtained.
Embodiment 2
[0019] 1) Preparation of pulverized coal additives: Add 8% sodium carbonate, 15% magnesium oxide, 15% silicon dioxide, 8% zinc oxide, 8% manganese dioxide, 6% barium oxide and 5% copper oxide was sequentially added and stirred for 20 minutes, then 30% activated calcium oxide and 5% ammonium bicarbonate were added and stirred for 10 minutes, and mixed uniformly to obtain a coal powder additive;
[0020] 2) Preparation of catalytic activator: stir 30% activated calcium oxide, 20% activated alumina, and 20% light burnt magnesium for 15 minutes according to mass percentage, then add 25% activated carbon and 5% calcium ammonium nitrate and stir. The catalyst activator is uniformly obtained.
Embodiment 3
[0022] 1) Preparation of pulverized coal additives: 18% sodium carbonate, 5% magnesium oxide, 14% silicon dioxide, 7% zinc oxide, 7% manganese dioxide, 8% barium oxide and 5% copper oxide was sequentially added and stirred for 20 minutes, then 28% activated calcium oxide and 8% ammonium bicarbonate were added and stirred for 10 minutes, and mixed uniformly to obtain a coal powder additive;
[0023] 2) Preparation of catalytic activator: stir 28% activated calcium oxide, 18% activated alumina, 20% calcined magnesium for 15 minutes, and then add 24% activated carbon and 10% calcium ammonium nitrate and stir evenly Get the catalytic activator.
PUM
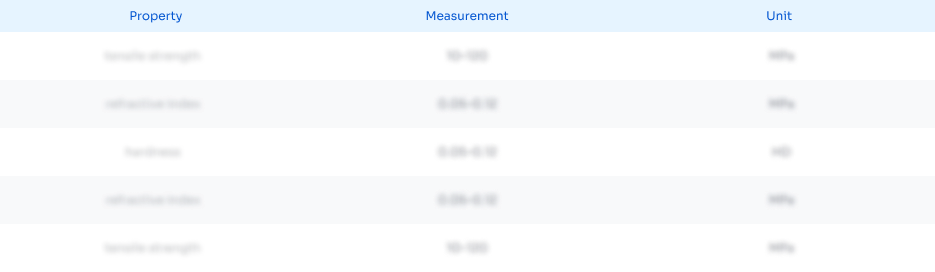
Abstract
Description
Claims
Application Information

- Generate Ideas
- Intellectual Property
- Life Sciences
- Materials
- Tech Scout
- Unparalleled Data Quality
- Higher Quality Content
- 60% Fewer Hallucinations
Browse by: Latest US Patents, China's latest patents, Technical Efficacy Thesaurus, Application Domain, Technology Topic, Popular Technical Reports.
© 2025 PatSnap. All rights reserved.Legal|Privacy policy|Modern Slavery Act Transparency Statement|Sitemap|About US| Contact US: help@patsnap.com