Solvent thermal polymerization method of methyl methacrylate-silicane copolymer
A technology of methyl methacrylate and silane copolymer, which is applied in the field of preparing methyl methacrylate-silane copolymer by solvothermal synthesis, can solve the problems of many operations required, complex synthesis process, harsh reaction conditions, etc., and achieve The reaction process is simple, the reaction activity is high, and the effect of complete reaction
- Summary
- Abstract
- Description
- Claims
- Application Information
AI Technical Summary
Problems solved by technology
Method used
Examples
Embodiment 1
[0021] Solvothermal Synthesis of Methyl Methacrylate-Maleic Anhydride-γ-Glycidyl Etheroxypropyltrimethoxysilane Copolymer
[0022] 5.09g of methyl methacrylate, 1.40g of γ-glycidyloxypropyltrimethoxysilane, 2.80g of maleic anhydride, and 0.05g of dicumyl peroxide were successively dissolved in 40mL of tetrahydrofuran solvent and mixed uniformly. Add the mixed solution into the autoclave, and seal it after blowing nitrogen for 3 minutes. Place the autoclave in a constant temperature box, react at 120° C. for 4 hours, take it out and cool it. After cooling, pour the product solution into anhydrous ethanol under stirring state to precipitate, then suction filter, wash with absolute ethanol and vacuum dry to obtain polymethyl methacrylate-maleic anhydride-γ-glycidoxy Propyltrimethoxysilane copolymer.
Embodiment 2
[0024] Solvothermal Synthesis of Methyl Methacrylate-Vinyl Trimethoxysilane Copolymer (No Synergistic Copolymer Monomer)
[0025] 8.20 g of methyl methacrylate, 1.70 g of vinyltrimethoxysilane, and 0.1 g of benzoyl peroxide were successively dissolved in 30 mL of xylene solvent and mixed uniformly. The mixed solution was added into the autoclave, and sealed after 4 minutes of nitrogen gas, the autoclave was placed in a constant temperature box, reacted at 80° C. for 8 hours, and was taken out for cooling. After cooling, pour the product solution into dehydrated ethanol under stirring state to precipitate, then suction filter, wash with dehydrated ethanol and vacuum dry to obtain polymethyl methacrylate-vinyltrimethoxysilane copolymer.
Embodiment 3
[0027] Solvothermal Synthesis of Methyl Methacrylate-γ-Methacryloyloxypropyltrimethoxysilane Copolymer
[0028] Dissolve 6.17g of methyl methacrylate, 6.00g of γ-methacryloxypropyltrimethoxysilane, 5.11g of acrylic acid, and 0.35g of azobisisobutyronitrile in 10mL of N,N-dimethylacetamide solvent In, mix well. Add the mixed solution into the autoclave, and seal it after passing nitrogen gas for 5 minutes. Place the autoclave in a constant temperature box, react at 65° C. for 12 hours, take it out and cool it. After cooling, pour the product solution into anhydrous ethanol under stirring state to precipitate, then suction filter, wash with absolute ethanol and dry in vacuum to obtain methyl methacrylate-γ-methacryloyloxypropyl trimethoxy silane copolymers.
PUM
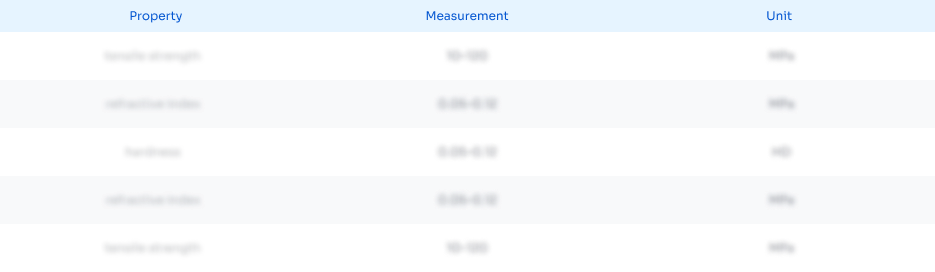
Abstract
Description
Claims
Application Information

- Generate Ideas
- Intellectual Property
- Life Sciences
- Materials
- Tech Scout
- Unparalleled Data Quality
- Higher Quality Content
- 60% Fewer Hallucinations
Browse by: Latest US Patents, China's latest patents, Technical Efficacy Thesaurus, Application Domain, Technology Topic, Popular Technical Reports.
© 2025 PatSnap. All rights reserved.Legal|Privacy policy|Modern Slavery Act Transparency Statement|Sitemap|About US| Contact US: help@patsnap.com