Method for preparing yttrium-doped nano aluminum nitride powder
A nano-aluminum nitride and yttrium-doped technology, which is applied in the field of material science, can solve problems such as the difficulty in achieving uniform mixing of additives and matrix materials, reducing the thermal conductivity of aluminum nitride ceramics, and increasing the content of sintering additives. Adverse effects, high density, effect of promoting dense sintering
- Summary
- Abstract
- Description
- Claims
- Application Information
AI Technical Summary
Problems solved by technology
Method used
Image
Examples
Embodiment 1
[0025] Weigh 1.0 mol of aluminum nitrate dissolved in 2.0 L of deionized water to form a 0.5 mol / L aluminum source solution, weigh 0.0076 mol of yttrium nitrate dissolved in 0.0152 L of deionized water to form a 0.5 mol / L of yttrium source solution, the above aluminum source The solution is mixed with the yttrium source solution to form an aluminum-yttrium mixed solution. Weigh 1.0 mol of citric acid and dissolve it in 5.0 mol of ethylene glycol, mix it evenly and add it to the aluminum-yttrium mixed solution. Weighed 0.83 mol of glucose and dissolved it in 1.66 L of deionized water to form a 0.5 mol / L carbon source solution, mixed it evenly and added it to the above aluminum-yttrium mixed solution. Stir the above mixed solution evenly, then raise the temperature to 130 °C for 2 h, continue to raise the temperature to 200 °C for 2 h, and obtain a fluffy brown-black powder after cooling. The above fluffy brown-black powder was calcined in a nitrogen atmosphere at 1000 °C for 1...
Embodiment 2
[0027] Weigh 1.0 mol of aluminum acetate and dissolve it in 1.0 L of absolute ethanol to form a 1.0 mol / L aluminum source solution, weigh 0.023 mol of yttrium nitrate and dissolve it in 0.023 L of absolute ethanol to form a 1.0 mol / L of yttrium source solution. The aluminum source solution and the yttrium source solution are mixed to form an aluminum-yttrium mixed solution. Weigh 2.0 mol of citric acid and dissolve it in 8.0 mol of ethylene glycol, mix and stir evenly, and then add it to the aluminum-yttrium mixed solution. Weigh 0.8 mol of sucrose and dissolve it in 0.8 L of absolute ethanol to form a 1.0 mol / L carbon source solution, mix it evenly and add it to the above aluminum-yttrium mixed solution. Stir the above mixed solution evenly, then heat up to 125 °C for 3 h, continue to heat up to 180 °C for 4 h, and obtain a fluffy brown-black powder after cooling. The above fluffy brown-black powder was calcined in a nitrogen atmosphere at 900 °C for 1 h to obtain a homogene...
Embodiment 3
[0029] Weigh 1.0 mol aluminum isopropoxide and dissolve in 0.5 L acetone to form a 2.0 mol / L aluminum source solution, weigh 0.03 mol yttrium acetate and dissolve it in 0.03 L acetone to form a 1.0 mol / L yttrium source solution, and dissolve the above aluminum source The solution is mixed with the yttrium source solution to form an aluminum-yttrium mixed solution. Weigh 1.5 mol of citric acid and dissolve it in 8.0 mol of ethylene glycol, mix and stir evenly, and then add it to the aluminum-yttrium mixed solution. Weigh 0.3 mol glucose and 0.3 mol sucrose and dissolve in 1.2 L deionized water to form a 0.5 mol / L carbon source solution, mix and stir evenly and add to the above aluminum-yttrium mixed solution. Stir the above mixed solution evenly, then heat up to 125 °C for 2 h, continue to heat up to 220 °C for 2 h, and get a fluffy brown-black powder after cooling. The above fluffy brown-black powder was calcined in a nitrogen atmosphere at 800 °C for 1 h to obtain a homogene...
PUM
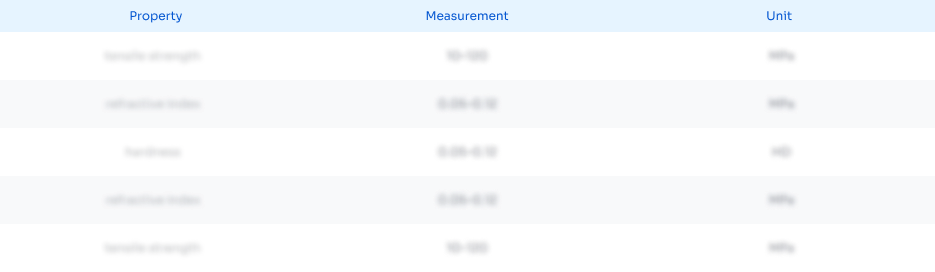
Abstract
Description
Claims
Application Information

- R&D
- Intellectual Property
- Life Sciences
- Materials
- Tech Scout
- Unparalleled Data Quality
- Higher Quality Content
- 60% Fewer Hallucinations
Browse by: Latest US Patents, China's latest patents, Technical Efficacy Thesaurus, Application Domain, Technology Topic, Popular Technical Reports.
© 2025 PatSnap. All rights reserved.Legal|Privacy policy|Modern Slavery Act Transparency Statement|Sitemap|About US| Contact US: help@patsnap.com