Polymerizing production method for transparent amorphous copolyester
A production method and technology of copolyester, which is applied in the field of polymerization production of transparent amorphous copolyester, can solve the problems of prolonging condensation reaction time and reducing catalytic activity, and achieve shortening of esterification time, reduction of terminal carboxyl group content and molecular weight distribution narrowing effect
- Summary
- Abstract
- Description
- Claims
- Application Information
AI Technical Summary
Problems solved by technology
Method used
Examples
Embodiment 1
[0032] 70 parts of PTA, 40 parts of EG, 15 parts of CHDM, monobutyltin oxide / dibutyltin oxide / ethylenediaminetetraacetic acid are 0.01 part / 0.04 part / 0.05 part, 0.05 part of phosphite tris(2,4- Di-tert-butylphenyl) ester antioxidant and 0.1 part of 2,2 methylene-bis(4-methyl-6-tert-butylphenol) antioxidant, 0.01 part of cobalt acetate and 0.06 part of antimony acetate / B Diaminetetraacetic acid (mass ratio 1:1) complex was beaten into slurry A.
[0033] Put the slurry A into the esterification kettle, fill it with nitrogen to 0.2MPa, raise the temperature to 220°C, control the pressure release rate, and maintain it at 0.3-0.35MPa. At normal pressure, the esterification time is 2h.
[0034] Press the esterified product into the condensation kettle, gradually raise the temperature to 250°C, reduce the reaction pressure to 0.4-0.5MPa, polymerize for 1.5-2 hours, then gradually reduce the pressure to less than 200Pa, and gradually reduce the temperature of the polycondensation rea...
Embodiment 2
[0036] In Example 1, after adding 0.05 part of triphenyl phosphite, the condensation reaction was carried out for 30 minutes, and the material was discharged to obtain a copolyester with an intrinsic viscosity of 0.83 dL / g and a carboxyl content of 7.3 mol / t.
Embodiment 3
[0038] 70 parts of PTA, 40 parts of EG, 20 parts of CHDM, monobutyltin oxide / dibutyltin oxide / ethylenediaminetetraacetic acid are 0.03 parts / 0.06 parts / 0.09 parts, 0.05 parts of phosphite tris(2,4- Di-tert-butylphenyl) ester antioxidant and 0.1 part of 2,2 methylene-bis(4-methyl-6-tert-butylphenol) antioxidant, 0.01 part of cobalt acetate and 0.06 part of ethylene glycol antimony / ethylenediaminetetraacetic acid (mass ratio 1:1) complex was beaten into slurry A.
[0039] Put the slurry A into the esterification kettle, fill it with nitrogen to 0.2MPa, raise the temperature to 220°C, control the pressure release rate, and maintain it at 0.3-0.35MPa. At normal pressure, the esterification time is 1.5h.
[0040] Press the esterified product into the condensation kettle, gradually raise the temperature to 250°C, reduce the reaction pressure to 0.4-0.5MPa, polymerize for 1.5-2 hours, then gradually reduce the pressure to less than 200Pa, and gradually reduce the temperature of the...
PUM
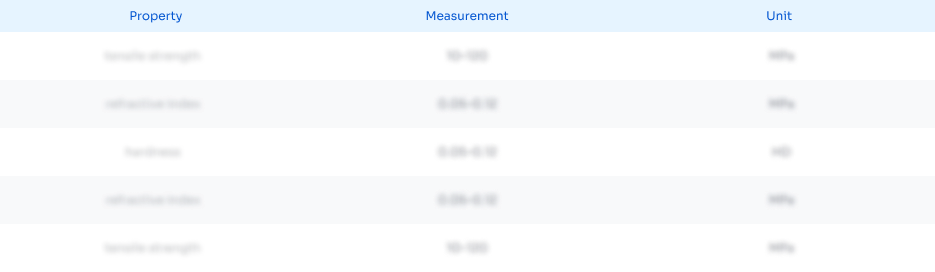
Abstract
Description
Claims
Application Information

- R&D Engineer
- R&D Manager
- IP Professional
- Industry Leading Data Capabilities
- Powerful AI technology
- Patent DNA Extraction
Browse by: Latest US Patents, China's latest patents, Technical Efficacy Thesaurus, Application Domain, Technology Topic, Popular Technical Reports.
© 2024 PatSnap. All rights reserved.Legal|Privacy policy|Modern Slavery Act Transparency Statement|Sitemap|About US| Contact US: help@patsnap.com