Flame retardant micro-foamed all plastic wood-like material and its preparation method
A wood-like material and micro-foaming technology, which is applied in the field of all-plastic wood-like materials and their preparation, can solve the problems of limited research reports, poor impact resistance, and easy burning of full-plastic wood-like materials, and reduce the difficulty of preparation technology , The flame retardant mechanism is simple, and the imitation wood effect is realistic
- Summary
- Abstract
- Description
- Claims
- Application Information
AI Technical Summary
Problems solved by technology
Method used
Image
Examples
Embodiment 1
[0024] Mix 1 part of nano-silicon carbide, 1 part of nano-calcium carbonate, and 10 parts of ABS resin, dry in a dryer at 80°C for 2 hours, and simultaneously add 0.5 parts of CF-210 / AC composite foaming agent (1:1) to 0.5 parts, 0.5 parts of ACR cell regulator, 15 parts of flame retardant HBCD / antimony trioxide / magnesium hydroxide (6:4:5), smoke suppressant zinc molybdate / iron oxide / zinc borate (2:1:2) 5 parts, 0.2 parts of UV-531 (ultraviolet absorber), 0.2 parts of polyethylene wax / lithium complex soap base (1:1), 0.4 parts of sandalwood oil, 0.7 parts of polybutyl acrylate, zinc oxide / iron oxide red / 0.5 parts of carbon black were mixed, and then the two groups of mixtures were mixed with 100 parts of PS and 25 parts of HIPS, and the final mixture was extruded and granulated in a twin-screw extruder (granulation extrusion temperature 160° C.), and finally the obtained granules The material is extruded and processed in an extruder (180°C, screw speed 6-10r / min).
[0025] T...
Embodiment 2
[0030] Mix 1 part of nano-barium sulfate, 2 parts of nano-calcium carbonate, and 13 parts of AS / PMMA resin (8:5), and dry in a dryer at 80° C. for 2 hours. At the same time, 1 part of CF-420 / AP composite blowing agent (4:5), 1 part of ACR cell regulator, 20 parts of flame retardant TBBPA / antimony trioxide / aluminum hydroxide (8:7:5), Smoke suppressant zinc molybdate / zinc oxide / aluminum hydroxide (5:3:2) 10 parts, UV-531 (ultraviolet absorber) 0.3 parts, calcium stearate / zinc stearate / amino silicone oil (1:1 : 0.3 part of 1), 0.4 part of cloudwood oil, 1 part of butyl polyacrylate, 1 part of benzidine yellow / quinacridone purple / permanent yellow HR (4:2:4), and then mix the two Mix the group mixture with 100 parts of PS and 30 parts of HIPS, extrude and granulate the final mixture in a twin-screw extruder (granulation extrusion temperature 170°C), and finally put the obtained pellets in the extruder (200°C, screw speed 6~10r / min) for extrusion processing.
[0031] The product w...
Embodiment 3
[0033] Mix 1.5 parts of nano-silica, 1.5 parts of nano-barium sulfate, 3 parts of nano-calcium carbonate, and 15 parts of ABS / AS / PMMA resin (6:6:3), and dry in a dryer at 80°C for 2 hours. At the same time blowing agent AP / AC / NaHCO 3 Composite (7:3:5) 1.5 parts, cell regulator PA-530 / K-400 composite (1:1) 2 parts, flame retardant DBDPO / decabromodiphenylethane / antimony trioxide / hydroxide Magnesium / aluminum hydroxide (5:6:4:5:5) 25 parts, zinc molybdate fume / iron oxide / cuprous oxide, zinc borate (5:3:3:4) 15 parts, UV-531 ( UV absorber) 0.5 parts, polyethylene wax / amino silicone oil (2:3) 0.5 parts, camphor wood sesame oil 0.7 parts, polybutyl acrylate 1.3 parts, zinc oxide / iron oxide red / carbon black, benzidine yellow, quinine Mix 1.5 parts of acridone purple and permanent yellow HR (2:3:1:4:2:3), then mix the two groups of mixtures with 100 parts of PS and 35 parts of HIPS, and put the final mixture in a twin-screw extruder (Pelleting extrusion temperature: 160°C) to extrude...
PUM
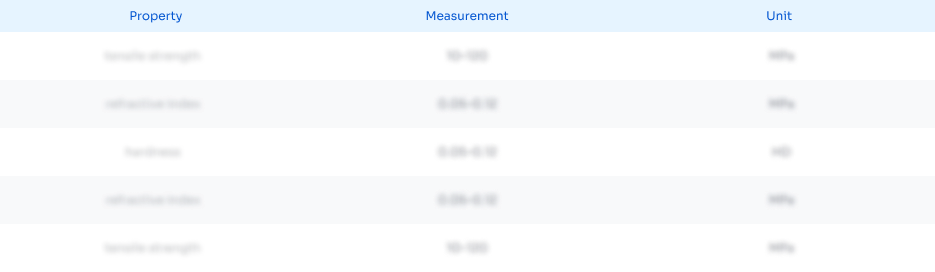
Abstract
Description
Claims
Application Information

- Generate Ideas
- Intellectual Property
- Life Sciences
- Materials
- Tech Scout
- Unparalleled Data Quality
- Higher Quality Content
- 60% Fewer Hallucinations
Browse by: Latest US Patents, China's latest patents, Technical Efficacy Thesaurus, Application Domain, Technology Topic, Popular Technical Reports.
© 2025 PatSnap. All rights reserved.Legal|Privacy policy|Modern Slavery Act Transparency Statement|Sitemap|About US| Contact US: help@patsnap.com