High-temperature resistant modified CPVC chemical tubing special-purpose material
A technology of copolymerization modification and plastic, applied in the field of modified polymer materials, can solve the problems of narrow processing temperature range, high melt viscosity, low impact strength of products, etc.
- Summary
- Abstract
- Description
- Claims
- Application Information
AI Technical Summary
Problems solved by technology
Method used
Examples
Embodiment 1
[0011] Embodiment 1: first 100 mass parts PVC, 0.5 mass parts dicumyl peroxide, 10 mass parts grafting monomer MMA and 3 mass parts composite stabilizers, 1.5 mass parts lubricants are fully mixed in a high-speed mixer, Then use two rollers to masticate at 185°C for 7 minutes and then release the sheet to obtain the final CPVC graft copolymerized modified plastic.
Embodiment 2
[0012] Embodiment 2: first 100 mass parts PVC, 0.8 mass parts dicumyl peroxide, 10 mass parts grafting monomer MMA and 3 mass parts composite stabilizer, 1.5 mass parts lubricant are fully mixed in high-speed mixer, Then use two rollers to masticate at 185°C for 7 minutes and then release the sheet to obtain the final CPVC graft copolymerized modified plastic.
Embodiment 3
[0013] Embodiment 3: first 100 mass parts PVC, 0.8 mass parts dicumyl peroxide, 10 mass parts grafting monomer MMA and 3 mass parts composite stabilizers, 1.5 mass parts lubricants are fully mixed in a high-speed mixer, Then use two rollers to masticate at 190°C for 7 minutes and then release the sheet to obtain the final CPVC graft copolymerized modified plastic.
PUM
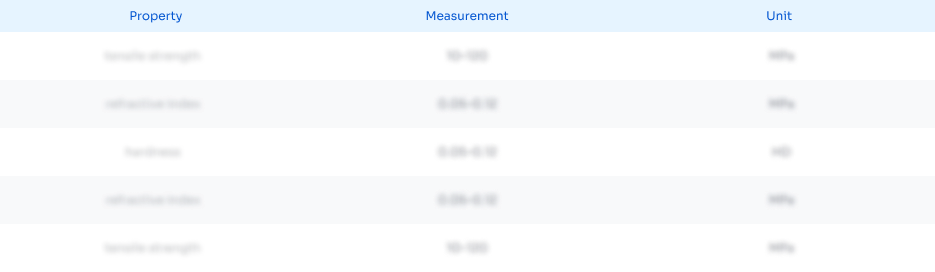
Abstract
Description
Claims
Application Information

- R&D
- Intellectual Property
- Life Sciences
- Materials
- Tech Scout
- Unparalleled Data Quality
- Higher Quality Content
- 60% Fewer Hallucinations
Browse by: Latest US Patents, China's latest patents, Technical Efficacy Thesaurus, Application Domain, Technology Topic, Popular Technical Reports.
© 2025 PatSnap. All rights reserved.Legal|Privacy policy|Modern Slavery Act Transparency Statement|Sitemap|About US| Contact US: help@patsnap.com