Multi-cycle quenching-partitioning-tempering (M Q-P-T) technique
A multi-cycle, process technology, applied in the direction of process efficiency improvement, manufacturing tools, heat treatment equipment, etc., can solve the problems of quenching cracking, plasticity, deficiency, etc.
- Summary
- Abstract
- Description
- Claims
- Application Information
AI Technical Summary
Problems solved by technology
Method used
Examples
Embodiment 1
[0014] 42CrMo shaft parts with a diameter of 150mm are processed by M Q-P-T process. It is required that the mechanical properties at 1 / 2R (R is the radius of the axis) from the surface after quenching and high temperature tempering are higher than a certain index. In the MQ-P-T process, water is used as the medium for fast cooling, and air is used for slow cooling.
[0015] According to the isothermal transformation cooling curve (TTT curve) of the workpiece material and the interface heat transfer coefficient and other parameters, the temperature field, tissue field and stress / strain field of the workpiece during the cooling process are numerically simulated. -20mm layer, 20-30mm layer, 30-35mm layer M Q-P-T process of Q-P-T transformation, that is, the first water quenching time is 180s, the first air cooling time is 20s, the second water quenching time is 120s, and the second time The air cooling time is 15s, the third water quenching time is 80s, and the third air co...
Embodiment 2
[0017] The 50mm thick micro-alloyed steel rolling plate is processed by the M Q-P-T process, and the M Q-P-T process is arranged after the rolling mill. It is required that the tensile strength and yield of the material from the surface to the thickness of 1 / 4 section thickness after the MQ-P-T process are determined to be higher than a certain index (that is, the structure mainly composed of tempered martensite is required), and the elongation and Low-temperature impact toughness is required. If the traditional rapid cooling method with one water spray will cause cracks on the surface of the rolled plate if the cooling time is too long, and the performance indicators will not meet the requirements if the cooling time is too short.
[0018] This embodiment solves this problem by using the MQ-P-T process. The medium used to achieve rapid cooling is water, and the medium used to achieve slow cooling is air. Rapid cooling is to arrange several sections of strong cooling zones...
Embodiment 3
[0021] The H13 mandrel with a diameter of 300mm is treated by the M Q-P-T process, and the mechanical properties of the material at 1 / 2R (R is the radius of the axis) from the surface after the M Q-P-T process are required to be higher than a certain value, and the polymer water-soluble medium is used to combine The M Q-P-T process handles the product.
[0022] First, according to the isothermal transformation cooling curve (TTT curve) of the workpiece material and the interface heat transfer coefficient and other parameters, the temperature field, tissue field and stress / strain field of the workpiece during the cooling process are numerically simulated. M Q-P-T process in which Q-P-T transformation occurs on the 0-20mm layer, 20-55mm layer, 55-65mm layer, and 65-75mm layer on the surface, that is, the first water quenching time is 300s, the first air cooling time is 120s, and the second water quenching time is 300s. The quenching time is 600s, the second air cooling time ...
PUM
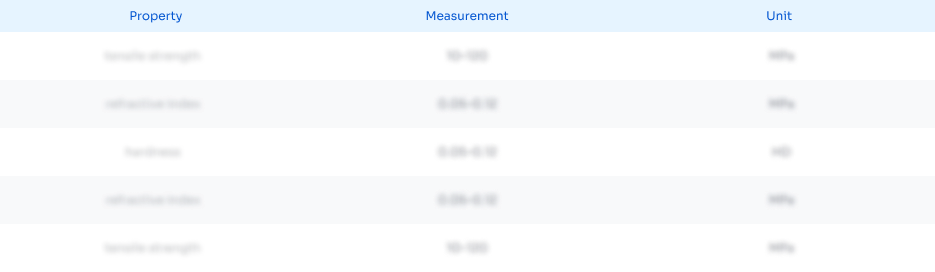
Abstract
Description
Claims
Application Information

- R&D
- Intellectual Property
- Life Sciences
- Materials
- Tech Scout
- Unparalleled Data Quality
- Higher Quality Content
- 60% Fewer Hallucinations
Browse by: Latest US Patents, China's latest patents, Technical Efficacy Thesaurus, Application Domain, Technology Topic, Popular Technical Reports.
© 2025 PatSnap. All rights reserved.Legal|Privacy policy|Modern Slavery Act Transparency Statement|Sitemap|About US| Contact US: help@patsnap.com