Lead-antimony rare-earth positive grid alloy and preparation method thereof
A positive plate and alloy technology, applied in the field of metallurgy, can solve the problems of capacity loss, deep discharge cycle life, environmental pollution, etc., and achieve the effects of long service life, reduced impedance, and excellent deep cycle performance
- Summary
- Abstract
- Description
- Claims
- Application Information
AI Technical Summary
Problems solved by technology
Method used
Image
Examples
Embodiment 1
[0042] Put 4.65Kg of pure lead into a lead-melting furnace (450°C-550°C) to melt, raise the temperature to 750-800°C, then add 0.35Kg of pure Sm, remove slag, stir, and keep warm at 650°C-700°C for 20 minutes Form Pb-7%Sm alloy;
[0043] Put 4.65Kg of pure lead into a lead-melting furnace (450°C-550°C) to melt it, raise the temperature to 770-820°C, add 0.35Kg of pure La, remove slag, stir, and keep it at 650°C-700°C for 20 minutes to form Pb-7%La alloy;
[0044] Put 98.99Kg of pure lead into a lead melting furnace (450°C-550°C) to melt, heat up to 500-600°C, add 1.01Kg of pure antimony with a purity of at least 99.95% and stir to form a Pb-1.009%Sb melt;
[0045] Take 72.14g of Pb-7%La master alloy and 927.86g of Pb-7%Sm master alloy and add them to the lead-antimony molten liquid in the above-mentioned lead melting furnace. After 30 minutes, a Pb-1%Sb-0.005%La-0.064%Sm alloy solution was obtained. Sampling and resampling, conforming to the casting mold after being release...
Embodiment 2
[0047] Put 4.65Kg of pure lead into a lead-melting furnace (450°C-550°C) to melt, heat up to 750-800°C, add 0.35Kg of pure Sm, remove slag, stir, and keep warm at 650°C-700°C for 20 minutes to form Pb-7%Sm alloy;
[0048] Put 4.65Kg of pure lead into a lead-melting furnace (450°C-550°C) to melt, heat up to 770-820°C, add 0.35Kg of pure La, remove slag, stir, and keep warm at 650°C-700°C for 20 minutes to form Pb-7%La alloy;
[0049] Put 99.961Kg of pure lead into a lead melting furnace (450°C-550°C) to melt, raise the temperature to 500-600°C, add 1.01Kg of pure antimony with a purity of at least 99.95% and stir to form a Pb-1.0%Sb melt;
[0050] Take 14.43g of Pb-7%La master alloy and 14.43g of Pb-7%Sm master alloy and add them to the lead-antimony molten liquid in the above-mentioned lead melting furnace. After 30 minutes, a Pb-1%Sb-0.001%La-0.001%Sm alloy solution was obtained. Sampling and resampling, conforming to the casting mold after being released from the furnace....
Embodiment 3
[0052] Put 9.3Kg of pure lead into a lead-melting furnace (450°C-550°C) to melt, heat up to 750-800°C, add 0.7Kg of pure Sm, remove slag, stir, and keep warm at 650°C-700°C for 20 minutes to form Pb-7%Sm alloy;
[0053] Put 9.3Kg of pure lead into a lead-melting furnace (450°C-550°C) to melt, raise the temperature to 770-820°C, add 0.7Kg of pure La, remove slag, stir, and keep warm at 650°C-700°C for 20 minutes to form Pb-7%La alloy;
[0054] Put 85.56Kg of pure lead into a lead melting furnace (450℃~550℃) to melt, heat up to 500~600℃, add 1.01Kg of pure antimony with a purity of at least 99.95% and stir to form Pb-1. 17%Sb melting liquid;
[0055] Take 7214.29g of Pb-7%La master alloy and 7214.29g of Pb-7%Sm master alloy, and add them to the lead-antimony melt in the above-mentioned lead melting furnace, after removing slag and stirring, the Insulated for 30 minutes to obtain a Pb-1%Sb-0.5%La-0.5%Sm alloy solution. Sampling and resampling, conforming to the casting mold a...
PUM
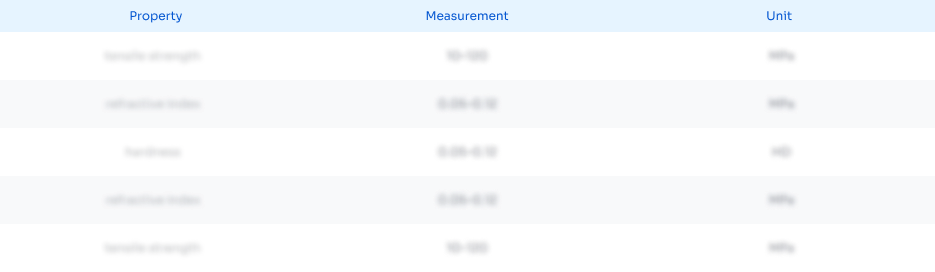
Abstract
Description
Claims
Application Information

- R&D
- Intellectual Property
- Life Sciences
- Materials
- Tech Scout
- Unparalleled Data Quality
- Higher Quality Content
- 60% Fewer Hallucinations
Browse by: Latest US Patents, China's latest patents, Technical Efficacy Thesaurus, Application Domain, Technology Topic, Popular Technical Reports.
© 2025 PatSnap. All rights reserved.Legal|Privacy policy|Modern Slavery Act Transparency Statement|Sitemap|About US| Contact US: help@patsnap.com