Heat treating method for driving roll and driving gear of rolling mill
A heat treatment method and technology for driving rollers, applied in heat treatment furnaces, heat treatment equipment, furnaces, etc., can solve the problems of insufficient impact resistance, high strength of driving teeth, broken teeth of driving rollers, etc.
- Summary
- Abstract
- Description
- Claims
- Application Information
AI Technical Summary
Problems solved by technology
Method used
Image
Examples
Embodiment
[0013] This embodiment deals with 6 φ173mm drive rollers used in Sendzimir mill, the material is X63CrMoV51.
[0014] This embodiment is the following sequential steps:
[0015] I After keeping the 6 driving rollers in a high temperature salt bath furnace at 1030°C for 45 minutes, they are hoisted into the quenching oil at a temperature of 50°C and cooled to 120°C.
[0016] II Then put the drive roller in a nitrate furnace at 560°C for three times of tempering, holding each time for 3.5 hours. After the first two tempering, it is naturally cooled to 60°C in air, and then the next tempering is performed; after the third tempering, it is cooled to room temperature in quenching oil. After testing, the hardness of the driving teeth of the two intermediate rollers after three tempering is 58-60HRC. One of the driving rollers is reserved for dissection test, and the sample number is 1.
[0017] III Perform local high temperature tempering on the driving teeth of the remaining 5 rolls, tha...
PUM
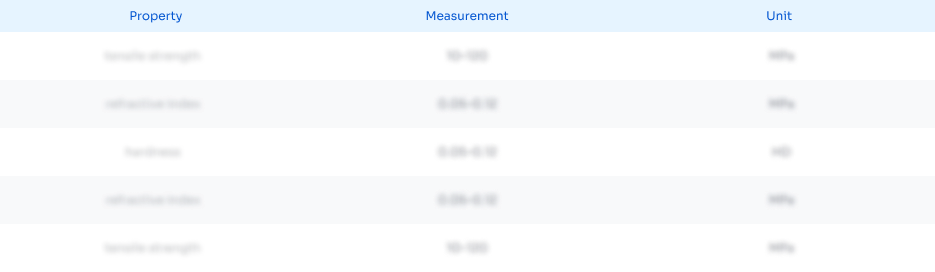
Abstract
Description
Claims
Application Information

- R&D Engineer
- R&D Manager
- IP Professional
- Industry Leading Data Capabilities
- Powerful AI technology
- Patent DNA Extraction
Browse by: Latest US Patents, China's latest patents, Technical Efficacy Thesaurus, Application Domain, Technology Topic, Popular Technical Reports.
© 2024 PatSnap. All rights reserved.Legal|Privacy policy|Modern Slavery Act Transparency Statement|Sitemap|About US| Contact US: help@patsnap.com