Formula and preparation method of composite low melting point nylon 6
A low-melting-point nylon technology, which is applied in the formulation and preparation of composite low-melting-point nylon 6, can solve problems such as the decrease in the added value of the mechanical properties of low-melting-point PA6 and the decrease in the dispersion effect of organic montmorillonite, and achieve low production costs and easy use. The effect is ideal and the effect of improving mechanical properties
- Summary
- Abstract
- Description
- Claims
- Application Information
AI Technical Summary
Problems solved by technology
Method used
Image
Examples
Embodiment 1
[0027] Embodiment 1 of the present invention: Preparation of composite low-melting nylon 6, calculated in parts by weight, first drying 90 parts of nylon 6 in a blast drying oven at 90°C for 12 hours, and drying 10 parts of organic montmorillonite at 80°C Dry in a blast drying oven for 24 hours, blend them and extrude through a twin-screw extruder, and then cut the extruded material into pellets; pre-dry 5 parts of anhydrous calcium chloride at 120 °C by blast drying Dry in the oven for 8 hours, then blend the obtained pellets with the anhydrous calcium chloride, extrude and cool through a twin-screw extruder, and then pelletize to obtain a finished product. In the production process, the screw speed of the twin-screw extruder is 210rpm, and the speed of the feeding screw is 15rpm. The temperature zone 1, temperature zone 2, temperature zone 3, temperature zone 4, temperature zone 5, temperature zone 6, There are seven temperature zones, eight temperature zones, and the temper...
Embodiment 2
[0028] Embodiment 2 of the present invention: preparation of composite low-melting nylon 6, calculated in parts by weight, first dry 92 parts of nylon 6 in a blast drying oven at 90°C for 12 hours, and mix 8 parts of organic montmorillonite at 80 ℃ in a blast drying oven for 24 hours, extrude their blends through a twin-screw extruder, and then pelletize the extruded materials; pre-dry 5.2 parts of anhydrous calcium chloride at 120 ℃ Dry in an air drying oven for 8 hours, then blend the obtained pellets with the anhydrous calcium chloride, extrude and cool through a twin-screw extruder, and then granulate to obtain a finished product. In the production process, the screw speed of the twin-screw extruder is 210 rpm, and the speed of the feeding screw is 15 rpm. The temperature is in the first zone, the second zone, the third zone, the fourth zone, the fifth zone, and the sixth zone. , seven temperature zones, eight temperature zones, the head temperature is 180°C, 190°C, 205°C,...
Embodiment 3
[0029] Embodiment 3 of the present invention: preparation of composite low-melting nylon 6, calculated in parts by weight, first dry 94 parts of nylon 6 in a blast drying oven at 90°C for 12 hours, and mix 6 parts of organic montmorillonite at 80 °C in a blast drying oven for 24 hours, extrude their blends through a twin-screw extruder, and then cut the extruded materials into pellets; blow 5.6 parts of anhydrous calcium chloride in advance at 120 °C Dry in an air drying oven for 8 hours, then blend the obtained pellets with the anhydrous calcium chloride, extrude and cool through a twin-screw extruder, and then granulate to obtain a finished product. In the production process, the screw speed of the twin-screw extruder is 210 rpm, and the speed of the feeding screw is 15 rpm. The temperature is in the first zone, the second zone, the third zone, the fourth zone, the fifth zone, and the sixth zone. , seven temperature zones, eight temperature zones, the head temperature is 180...
PUM
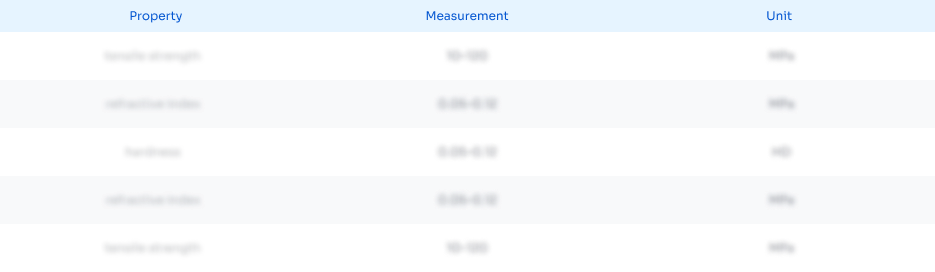
Abstract
Description
Claims
Application Information

- R&D Engineer
- R&D Manager
- IP Professional
- Industry Leading Data Capabilities
- Powerful AI technology
- Patent DNA Extraction
Browse by: Latest US Patents, China's latest patents, Technical Efficacy Thesaurus, Application Domain, Technology Topic, Popular Technical Reports.
© 2024 PatSnap. All rights reserved.Legal|Privacy policy|Modern Slavery Act Transparency Statement|Sitemap|About US| Contact US: help@patsnap.com