The preparation method of malonate
A technology of malonate and malonate, applied in the field of malonate preparation, which can solve the problems of incomplete esterification, high requirements for stirring equipment, and poor dispersion
- Summary
- Abstract
- Description
- Claims
- Application Information
AI Technical Summary
Problems solved by technology
Method used
Examples
Embodiment 1
[0032] Weigh 95g (1.0mol) of chloroacetic acid and dissolve it in 48g of water, adjust the pH to 6.5-7.5 with 216g of 25% saturated sodium carbonate solution at 20°C to form a sodium chloroacetate solution. Add this solution to 196g of 30% sodium cyanide solution, raise the temperature to 50°C to trigger the cyanation reaction, stop heating when the temperature reaches 85-90°C, let it react naturally to the highest temperature and then cool down rapidly, and react at 93°C for 0.5 ~1h to stop the reaction. After the reaction solution drops to a certain temperature, add 150g of 40% liquid caustic soda, react at 105-110°C under a slight negative pressure for 4-5 hours, cool to room temperature, neutralize the solution with 45g of concentrated hydrochloric acid to PH=8, and the feed liquid settles for 1 ~2h, filter to remove 4g of organic flocs. The filtrate was concentrated under vacuum at 100°C to obtain 550g of water, then 295.9g of concentrated hydrochloric acid was added to ...
Embodiment 2
[0035]Dissolve 95g (1.0mol) of chloroacetic acid in 48g of water, and adjust the pH to 6.5-7.5 with 216g of 25% saturated sodium carbonate solution at 20°C to form a sodium chloroacetate solution.
[0036] Take by weighing the liquid sodium cyanide 219.2g (26.82% of sodium cyanide content, 6.85% of sodium carbonate content, 1.65% of sodium hydroxide content) of the liquid sodium cyanide prepared by Angle method hydrogen cyanide synthesis gas and sodium hydroxide reaction, according to the The residual alkali (sodium carbonate and sodium hydroxide) analysis data is calculated as the residual alkali amount is 0.1%, and the amount of anhydrous calcium chloride is added. Sodium cyanide and calcium chloride were reacted for 0.5h at 30°C, and the residual alkali in sodium cyanide was analyzed to be less than 0.5%.
[0037] Add sodium chloroacetate solution to the treated sodium cyanide suspension, raise the temperature to 50°C to initiate the cyanation reaction, stop heating when th...
Embodiment 3
[0039] Replace methanol with 138g of ethanol, all the other are the same as in Example 2, finally obtain 143.2g of product, the content of diethyl malonate is 99.1% through gas chromatography analysis, and the yield is 89.5%.
PUM
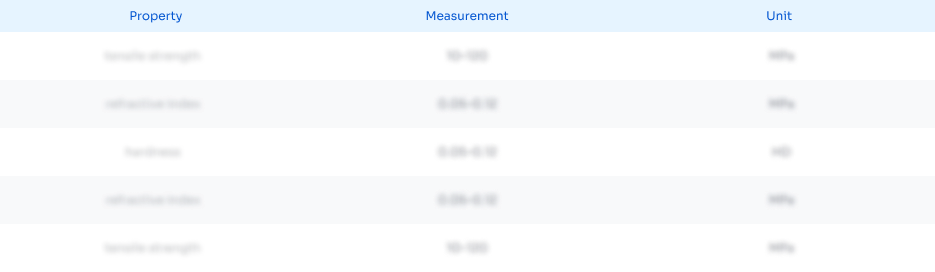
Abstract
Description
Claims
Application Information

- R&D
- Intellectual Property
- Life Sciences
- Materials
- Tech Scout
- Unparalleled Data Quality
- Higher Quality Content
- 60% Fewer Hallucinations
Browse by: Latest US Patents, China's latest patents, Technical Efficacy Thesaurus, Application Domain, Technology Topic, Popular Technical Reports.
© 2025 PatSnap. All rights reserved.Legal|Privacy policy|Modern Slavery Act Transparency Statement|Sitemap|About US| Contact US: help@patsnap.com