Method for producing potassium manganite or sodium manganate
A technology for the production of potassium manganate and sodium manganate, applied in the direction of manganate/permanganate, etc., can solve the problems of high requirements on equipment structure and compressive performance, unsuitable manganese carbonate ore resources, etc., to shorten the production cycle , good adaptability, the effect of improving conversion rate
- Summary
- Abstract
- Description
- Claims
- Application Information
AI Technical Summary
Problems solved by technology
Method used
Image
Examples
Embodiment 1
[0023] (1) Crush 500g of pyrolusite with a manganese content of 35% to -200 mesh and account for 70% of the content, weigh 392g of potassium hydroxide, add 350ml of water, stir to dissolve the potassium hydroxide, in which the alkali concentration is 53%, add manganese ore Powder and stir to form a paste, put it into a roasting furnace, and sinter at 400°C for 1h, and the manganese-alkali molar ratio of the pyrolusite to potassium hydroxide is 1:2.2;
[0024] (2) Pulverizing the sintered ore obtained in step (1), so that the -200 mesh content accounts for 70%;
[0025] (3) Put the fine-grained powder ore in the step (2) into a fluidized bed reactor, feed air to keep the material in a suspended state, and keep the water content in the air at 50g / m 3 , Oxidative roasting at 220 ° C for 2h.
[0026] (4) Dissolving the roasted product in the step (3), the amount of water added is twice the mass of the roasted product, the stirring speed is 10r / min, the stirring time is 10min, and...
Embodiment 2
[0028] (1) Grind 500g of pyrolusite with a manganese content of 50% until the -200 mesh content accounts for 72%, weigh 473g of sodium hydroxide, stir and mix the two materials, put them in a roaster, and sinter at 350°C for 1h , the manganese alkali mol ratio of described pyrolusite and sodium hydroxide is 1:2.6;
[0029] (2) Pulverizing the sintered ore obtained in step (1), so that the -200 mesh content accounts for 70%;
[0030] (3) Put the fine-grained powder ore in the step (2) into a fluidized bed reactor, feed oxygen to keep the material in a suspended state, and keep the water content in the oxygen at 100g / m 3 , Oxidative roasting at 240 ° C for 1 h.
[0031] (4) Dissolving the roasted product in the step (3), the amount of water added is 2.5 times the quality of the roasted product, the stirring speed is 10r / min, the stirring time is 10min, and the solid-liquid separation is carried out. The obtained solid phase is mainly un The manganese dioxide of reaction, the g...
Embodiment 3
[0033] (1) Crush 650g of manganese carbonate with a manganese content of 30% to -200 mesh and account for 75%, weigh 556g of potassium hydroxide, add 550ml of water, and stir to dissolve the potassium hydroxide. The alkali concentration is 50%, and add manganese ore Powder and stir to form a paste, put it into a roasting furnace, and sinter at 800°C for 1.5h, and the manganese-alkali molar ratio of the manganese carbonate to potassium hydroxide is 1:2.8;
[0034] (2) Pulverizing the sintered ore obtained in step (1), so that the -200 mesh content accounts for 75%;
[0035] (3) Put the fine-grained powder ore in the step (2) into a fluidized bed reactor, feed in heated chlorine gas to keep the material in a suspended state, and keep the volume fraction of nitrogen in the chlorine gas at 70%, at 250°C Oxidation roasting 1h.
[0036] (4) Dissolve the roasted product in the step (3), add water 3 times the mass of the roasted product, stir at a speed of 10r / min, stir for 15min, an...
PUM
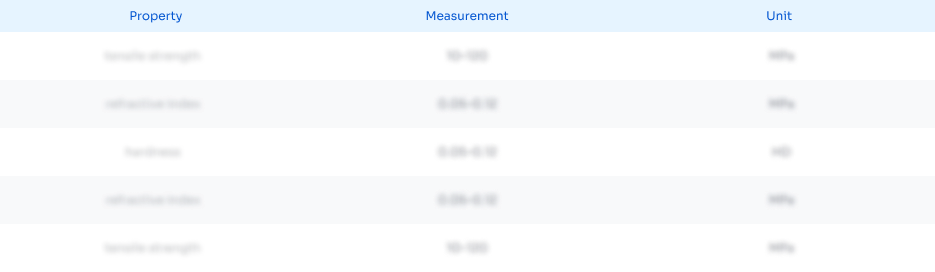
Abstract
Description
Claims
Application Information

- Generate Ideas
- Intellectual Property
- Life Sciences
- Materials
- Tech Scout
- Unparalleled Data Quality
- Higher Quality Content
- 60% Fewer Hallucinations
Browse by: Latest US Patents, China's latest patents, Technical Efficacy Thesaurus, Application Domain, Technology Topic, Popular Technical Reports.
© 2025 PatSnap. All rights reserved.Legal|Privacy policy|Modern Slavery Act Transparency Statement|Sitemap|About US| Contact US: help@patsnap.com