Heat transfer printing process for patterns by using calcium silicate board
A calcium silicate board and thermal transfer printing technology, which is applied in printing, copying/marking methods, etc., can solve the problems of wasting human resources, wasting resources and energy, and low work efficiency, so as to reduce production costs, save resources and energy, The effect of improving work efficiency
- Summary
- Abstract
- Description
- Claims
- Application Information
AI Technical Summary
Problems solved by technology
Method used
Image
Examples
Embodiment approach
[0022] As an embodiment of the present invention, see figure 1 , the present invention includes a calcium silicate plate heat transfer pattern process, including plate pretreatment, plate surface treatment and plate surface thermal transfer, the plate pretreatment includes thickness sanding and dust removal; the plate surface treatment includes Flow coating, flattening and drying; heat transfer on the surface of the board includes coating primer, drying, primer sanding, roller fluorocarbon primer, drying, covering heat transfer paper and heat transfer.
[0023] The specific process of the plate pretreatment is:
[0024] a. Fixed-thickness sanding: After manual loading, use a fixed-thickness sander to move the plate at a linear speed of 5m / min, an abrasive belt of 180~240 mesh, and a speed of 1000r / min, for constant-thickness sanding. The sanding thickness is 10μm, precision The graphite belt speed is 1000r / min for polishing;
[0025] b. Dust removal: Use a roller brush to re...
PUM
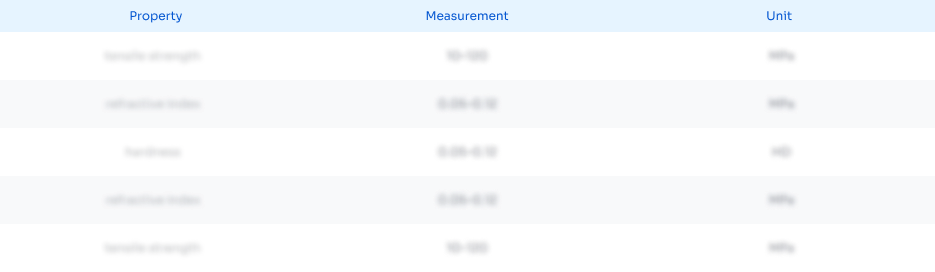
Abstract
Description
Claims
Application Information

- R&D Engineer
- R&D Manager
- IP Professional
- Industry Leading Data Capabilities
- Powerful AI technology
- Patent DNA Extraction
Browse by: Latest US Patents, China's latest patents, Technical Efficacy Thesaurus, Application Domain, Technology Topic, Popular Technical Reports.
© 2024 PatSnap. All rights reserved.Legal|Privacy policy|Modern Slavery Act Transparency Statement|Sitemap|About US| Contact US: help@patsnap.com