Silanization treatment method before coating of steel piece
A technology of silanization treatment and silanization, which is applied in the direction of metal material coating process, etc., to achieve the effects of enhancing bonding strength, improving coating bonding force, and improving corrosion resistance and aging resistance.
- Summary
- Abstract
- Description
- Claims
- Application Information
AI Technical Summary
Problems solved by technology
Method used
Examples
Embodiment 1
[0042] 1. Material preparation: Q235 steel sheet, using conventional grinding, sandblasting and polishing, sandblasting the surface of the steel part with a dry sandblasting machine for grinding, polishing the surface of the sample with a water polishing machine, SiC sandpaper Grind to 600#.
[0043] 2. Degreasing: NaOH 50g / L, NaOH 2 CO 3 25g / L, Na 3 PO 4 12H 2 O 30g / L, Na 2 SiO 3 12g / L, the balance is water, the temperature is 80-90°C, and the time is to remove the oil. After degreasing, the test piece is rinsed with natural water, and then rinsed with deionized water.
[0044] 3. Soak in silane solution: The silane solution is prepared by coupling agent KH560, deionized water and anhydrous methanol in a weight ratio of 12:16:72. First, anhydrous methanol and deionized water are prepared into an alcohol-water solution, and formic acid is added to adjust the pH to 4.5-5.5, and the coupling agent KH560 is added under stirring, and the silanol solution is obtained after...
Embodiment 2
[0049] The difference from Example 1 is:
[0050] 1. Material preparation: A32 steel sheet, using conventional grinding, sandblasting, polishing, and SiC sandpaper grinding to 600#.
[0051] 2. Degreasing: NaOH 100g / L, NaOH 2 CO 3 60g / L, Na 3 PO 4 12H 2 O 15g / L, Na 2 SiO 3 15g / L, the balance is water, the temperature is 80-90°C, the time is to remove the oil, after degreasing, the test piece is rinsed with natural water, and then rinsed with deionized water.
[0052] 3. Soak in silane solution: The silane solution is prepared by coupling agent KH560, deionized water and anhydrous methanol in a weight ratio of 5:10:85. First, anhydrous methanol and deionized water are prepared into an alcohol-water solution, and formic acid is added to adjust the pH to 4.5-5.5, and the coupling agent KH560 is added under stirring, and the silanol solution is obtained after hydrolysis for 1 hour. Immerse the test piece in the silanol solution for 0.5-2 minutes, take it out, and let it ...
Embodiment 3
[0057] The difference from Example 1 is:
[0058] 1. Material preparation: Q235q steel sheet, using conventional grinding, sandblasting, polishing, and SiC sandpaper grinding to 600#.
[0059] 2. Degreasing: NaOH 60g / L, NaOH 2 CO 3 20g / L, Na 3 PO 4 12H 2 O 20g / L, Na 2 SiO 3 5g / L, the balance is water, the temperature is 80-90°C, and the time is to remove the oil. After degreasing, the test piece is rinsed with natural water, and then rinsed with deionized water.
[0060] 3. Soak in silane solution: The silane solution is prepared by coupling agent KH550, deionized water and absolute ethanol in a weight ratio of 2:5:93. First, prepare an alcohol-water solution with absolute ethanol and deionized water, add acetic acid to adjust the pH to 3.5-5.0, add coupling agent KH550 under stirring, and hydrolyze for 2 hours to form a silanol solution. Immerse the test piece in the silanol solution for 0.5-2 minutes, take it out, and let it dry naturally.
[0061] 4. Drying: Dry th...
PUM
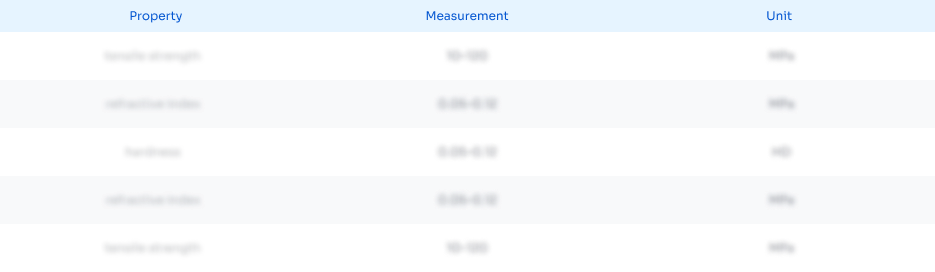
Abstract
Description
Claims
Application Information

- R&D
- Intellectual Property
- Life Sciences
- Materials
- Tech Scout
- Unparalleled Data Quality
- Higher Quality Content
- 60% Fewer Hallucinations
Browse by: Latest US Patents, China's latest patents, Technical Efficacy Thesaurus, Application Domain, Technology Topic, Popular Technical Reports.
© 2025 PatSnap. All rights reserved.Legal|Privacy policy|Modern Slavery Act Transparency Statement|Sitemap|About US| Contact US: help@patsnap.com