Method for preparing hard alloy materials
A cemented carbide and hard phase technology, applied in the field of cemented carbide materials, can solve the problems of WC grain growth, poor cobalt oxidation resistance and corrosion resistance, and cemented carbide cannot adapt to the working environment. Achieve the effect of low manufacturing cost and stable quality
- Summary
- Abstract
- Description
- Claims
- Application Information
AI Technical Summary
Problems solved by technology
Method used
Examples
Embodiment 1
[0011] The present invention comprises the following steps,
[0012] (1), get the raw material of following weight percent, the composite hard phase tungsten carbide powder 10% of 10-15 micron particle, the composite hard phase tungsten carbide powder 30% of 5-10 micron particle, the 1.0-1.5 micron particle Composite hard phase tungsten carbide powder 30%, chromium carbide powder 1.5%, cobalt powder 28.5%;
[0013] (2) The raw materials are mixed according to the proportion, ground, pressed and formed, and then kept at 1500°C for 30 minutes to obtain the cemented carbide material.
Embodiment 2
[0015] It includes the following steps,
[0016] (1), get the raw material of following weight percentage, the composite hard phase tungsten carbide powder 15% of 10-15 micron particle, the composite hard phase tungsten carbide powder 30% of 5-10 micron particle, the 1.0-1.5 micron particle Composite hard phase tungsten carbide powder 25%, chromium carbide powder 2%, cobalt powder 28%;
[0017] (2) The raw materials are mixed according to the proportion, ground, pressed and formed, and then kept at 1600° C. for 30 minutes to obtain the cemented carbide material.
Embodiment 3
[0019] It includes the following steps,
[0020] (1), get the raw material of following weight percent, the composite hard phase tungsten carbide powder 20% of 10-15 micron particle, the composite hard phase tungsten carbide powder 28% of 5-10 micron particle, the 1.0-1.5 micron particle Composite hard phase tungsten carbide powder 25%, chromium carbide powder 1.5%, cobalt powder 25.5%;
[0021] (2) The raw materials are mixed according to the proportion, ground, pressed and formed, and then kept at 1550° C. for 30 minutes to obtain the cemented carbide material.
PUM
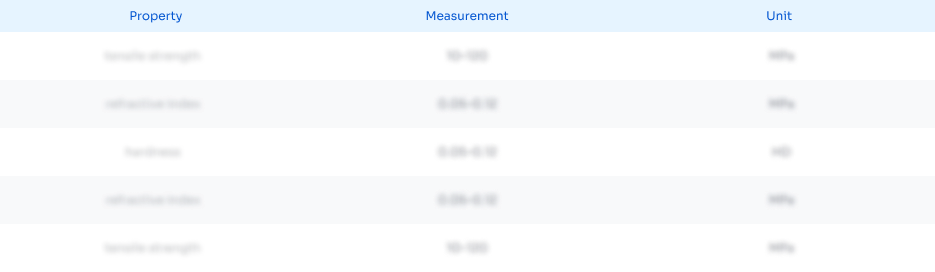
Abstract
Description
Claims
Application Information

- Generate Ideas
- Intellectual Property
- Life Sciences
- Materials
- Tech Scout
- Unparalleled Data Quality
- Higher Quality Content
- 60% Fewer Hallucinations
Browse by: Latest US Patents, China's latest patents, Technical Efficacy Thesaurus, Application Domain, Technology Topic, Popular Technical Reports.
© 2025 PatSnap. All rights reserved.Legal|Privacy policy|Modern Slavery Act Transparency Statement|Sitemap|About US| Contact US: help@patsnap.com