Novel process for separating zinc and cobalt from nickel and cobalt slag from zinc smelting and purification
A nickel-cobalt slag and zinc smelting technology, applied in the field of comprehensive recycling of nickel-cobalt slag, can solve environmental pollution, no separation technology, large zinc powder and other problems, and achieve the effect of solving industry problems
- Summary
- Abstract
- Description
- Claims
- Application Information
AI Technical Summary
Problems solved by technology
Method used
Image
Examples
Embodiment 1
[0021] Example 1: see figure 1 A zinc-cobalt separation process for purifying nickel-cobalt slag produced by zinc smelting, the steps are:
[0022] (1) One-stage leaching: Slurry the nickel-cobalt slag with water and add it to the leaching tank. The leaching tank is equipped with a natural exhaust pipe, and then sulfuric acid is added. The initial concentration of sulfuric acid in the reaction solution is controlled at 120-130g / L. The solid ratio is 3 / 1, stirred, the heating temperature is 70-75°C, the reaction time is 110 minutes, and then filtered to obtain a section of leaching solution and a section of leaching residue;
[0023] (2) Second-stage leaching: Slurry the first-stage leaching residue with water and add it to the leaching tank. The leaching tank is equipped with a natural exhaust pipe, and then sulfuric acid is added. The initial concentration of sulfuric acid in the reaction solution is controlled at 195-200g / L. The liquid-solid ratio is 3 / 1, stirred, the heati...
Embodiment 2
[0034] Example 2: see figure 1 A zinc-cobalt separation process for purifying nickel-cobalt slag produced by zinc smelting, the steps are:
[0035] (1) One-stage leaching: Slurry the nickel-cobalt slag with water and add it to the leaching tank. The leaching tank is equipped with a natural exhaust pipe, and then sulfuric acid is added. The initial concentration of sulfuric acid in the reaction solution is controlled at 130-135g / L. The solid ratio is 4 / 1, stirred, the heating temperature is 75-80°C, the reaction time is 90 minutes, and then filtered to obtain a section of leaching solution and a section of leaching residue;
[0036] (2) Second-stage leaching: Slurry the first-stage leaching residue with water and add it to the leaching tank. The leaching tank is equipped with a natural exhaust pipe, and then sulfuric acid is added. The initial concentration of sulfuric acid in the reaction solution is controlled at 195-200g / L. The liquid-solid ratio is 4 / 1, stirring, the heati...
Embodiment 3
[0048] Embodiment 3: see figure 1 , step is the same as embodiment 2, but described activator is made up of following components by weight percentage: ZnO 33%, Na 2 o 2 32%, Na 2 SO 4 35%.
[0049] The inorganic coagulant consists of the following components by weight percentage: ZnCO 3 2Zn(OH) 2 ·H 2 O60%, NaOH 40%.
PUM
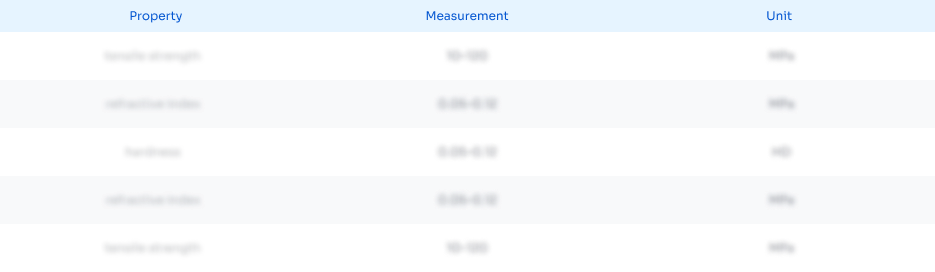
Abstract
Description
Claims
Application Information

- R&D
- Intellectual Property
- Life Sciences
- Materials
- Tech Scout
- Unparalleled Data Quality
- Higher Quality Content
- 60% Fewer Hallucinations
Browse by: Latest US Patents, China's latest patents, Technical Efficacy Thesaurus, Application Domain, Technology Topic, Popular Technical Reports.
© 2025 PatSnap. All rights reserved.Legal|Privacy policy|Modern Slavery Act Transparency Statement|Sitemap|About US| Contact US: help@patsnap.com