A method for combined treatment of acid leaching slag by separation and metallurgy
A combination of dressing and smelting, acid leaching slag technology, applied in the direction of improvement of process efficiency, etc., can solve the problems of high energy consumption of pyro-smelting process, low enrichment rate of flotation process, secondary pollution, etc., so as to achieve no secondary pollution secondary pollution, elimination of heavy metal pollution, and improvement of economic benefits
- Summary
- Abstract
- Description
- Claims
- Application Information
AI Technical Summary
Problems solved by technology
Method used
Image
Examples
Embodiment 1
[0018] (1) Re-election: Put 100kg of acid leaching residue and water into a ball mill at a liquid-solid ratio of 1:1 for ball milling. After ball milling to -200 mesh accounting for 50%, add it to a drum-shaped dense medium separator for re-election. 2% ferrosilicon ore was added to the mixture, and the gravity separation time was 20 minutes to obtain heavy separation concentrate and light tailings. After the light tailings were thickened, the supernatant and silica sand were obtained. ;
[0019] (2) Acidification roasting-water washing-concentrated crystallization: mix 5% concentrated sulfuric acid into the concentrate and add it to the rotary kiln for roasting, control the roasting temperature at 700°C, roasting time for 2 hours, wash the obtained calcined sand with tap water, and wash the slag with a section of water Silver-rich lead slag and iron sulfate solution, iron sulfate solution and silver-rich lead slag are washed in two stages respectively, silver-rich lead slag i...
Embodiment 2
[0023] (1) Re-election: Put 100kg of acid leaching residue and water into the ball mill according to the liquid-solid ratio of 1:1 for ball milling. After ball milling to -200 mesh accounting for 80%, add it to the drum-shaped dense medium separator for re-election. 4% ferrosilicon ore was added to the mixture, and the gravity separation time was 50 minutes to obtain the gravity separation concentrate and light tailings. After the light tailings were dense, the supernatant and silica sand were obtained, and the gravity separation concentrate was dense to obtain the concentrate and supernatant. ;
[0024] (2) Acidification roasting-water washing-concentrated crystallization: mix 8% concentrated sulfuric acid into the concentrate and add it to the rotary kiln for roasting, control the roasting temperature at 900°C, roasting time 1.5h, wash the obtained calcined sand with tap water, and wash with water for a period of time Slag silver-rich lead slag and iron sulfate solution, iro...
Embodiment 3
[0028] (1) Re-election: Put 100kg of acid leaching residue and water into the ball mill according to the liquid-solid ratio of 1:1 for ball milling. After ball milling to -200 mesh accounting for 90%, add it to the drum-shaped dense medium separator for re-election. Add 5% ferrosilicon ore to the mixture, and the gravity separation time is 30 minutes to obtain the gravity separation concentrate and light tailings. After the light tailings are dense, the supernatant and silica sand are obtained. After the gravity separation concentrate is dense, the concentrate and supernatant are obtained. ;
[0029] (2) Acidification roasting-water washing-concentrated crystallization: mix 5% concentrated sulfuric acid into the concentrate and add it to the rotary kiln for roasting, control the roasting temperature at 1000°C, roasting time 1h, wash the obtained calcined sand with tap water, and wash the slag with a section of water Silver-rich lead slag and iron sulfate solution, iron sulfate...
PUM
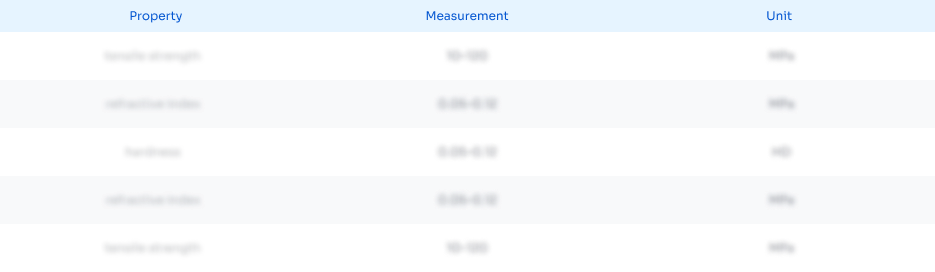
Abstract
Description
Claims
Application Information

- R&D
- Intellectual Property
- Life Sciences
- Materials
- Tech Scout
- Unparalleled Data Quality
- Higher Quality Content
- 60% Fewer Hallucinations
Browse by: Latest US Patents, China's latest patents, Technical Efficacy Thesaurus, Application Domain, Technology Topic, Popular Technical Reports.
© 2025 PatSnap. All rights reserved.Legal|Privacy policy|Modern Slavery Act Transparency Statement|Sitemap|About US| Contact US: help@patsnap.com