Method for preparing graphene loaded ferroferric oxide magnetic nanometer particle composite material
A technology of magnetic nanoparticles and ferroferric oxide, which is applied in the direction of material electrochemical variables, electrodes, electrolysis process, etc., can solve the problems of time-consuming and labor-intensive preparation and purification, easy degradation, and the variability of natural enzymes, etc., and achieve excellent electrocatalytic activity , Particle distribution is uniform, the effect of uniform distribution
- Summary
- Abstract
- Description
- Claims
- Application Information
AI Technical Summary
Problems solved by technology
Method used
Image
Examples
Embodiment 1
[0033]Get graphite powder and sodium nitrate, then add glacial sulfuric acid with a concentration of 98wt% and stir evenly, then put it in an ice bath, slowly add potassium permanganate while stirring, at this time, the temperature is always kept below 20°C, and then heat up to 35±5°C and keep warm for 1~2h. After the reaction, slowly add deionized water, raise the temperature to 85~95°C, keep warm for 15min, then add 10ml of hydrogen peroxide and deionized water with a mass fraction of 30%. Centrifugal, 5wt% HCl wash, dry, grind, finally obtain graphite oxide powder; Wherein the mass ratio of graphite powder and sodium nitrate is 2: 1, the ratio of glacial sulfuric acid and graphite powder is 23ml / mg, potassium permanganate and graphite The mass ratio of powder is 3:1, the volume ratio of deionized water and concentrated sulfuric acid added for the first time is 2:1, and the volume ratio of deionized water and concentrated sulfuric acid added for the second time is 6:1.
[00...
Embodiment 2
[0036] Weigh 220mg of graphite oxide (commercially available) and add it to a beaker, then add 220ml of deionized water, ultrasonically disperse for 80min, then centrifuge to remove unflaked graphite flakes to obtain an aqueous solution of graphene oxide, pour the solution into a three-necked flask, and add 2.2ml of mass The fraction is 85% hydrazine hydrate and 0.11g SDBS, magnetically stirred and heated to 110°C, condensed and refluxed for 22h. After the reaction, dry the modified graphene dispersion and add water to 50ml, ultrasonically disperse, centrifuge to remove large particles in the solution, and then pour it into a three-necked flask. Then weigh 0.3784g of ferric chloride and 0.1391g of ferrous chloride tetrahydrate in 50ml of deionized water, feed nitrogen to the aqueous solution for 20min, and then add Fe 3+ and Fe 2+ The aqueous solution of the mixture was poured into the above-mentioned graphene dispersion liquid, and after ultrasonic stirring for 10 min, 8M am...
Embodiment 3
[0038] Weigh 240mg of pre-prepared graphite oxide and add it to a beaker, then add 240ml of deionized water, ultrasonically disperse for 100min, and then centrifuge to remove unexfoliated graphite flakes to obtain an aqueous solution of graphene oxide, pour the solution into a three-necked flask, and add 2.4ml of mass fraction 85% hydrazine hydrate and 0.12gPSS, magnetically stirred and heated to 120°C, condensed and refluxed for 24h. After the reaction, dry the modified graphene dispersion and add water to 50ml, ultrasonically disperse, centrifuge to remove large particles in the solution, and then pour it into a three-necked flask. Then take by weighing 0.4865g ferric chloride and 0.1789g ferrous chloride tetrahydrate in 50ml deionized water, feed nitrogen into the aqueous solution for 30min, and then add Fe 3+ and Fe 2+ The aqueous solution of the mixture was poured into the above-mentioned graphene dispersion liquid, and after ultrasonic stirring for 10 min, 8M ammonia so...
PUM
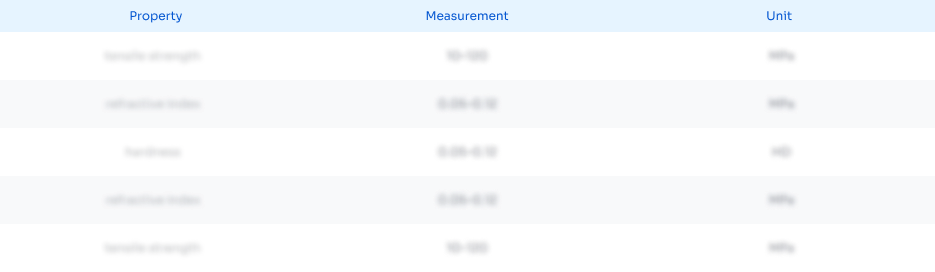
Abstract
Description
Claims
Application Information

- R&D
- Intellectual Property
- Life Sciences
- Materials
- Tech Scout
- Unparalleled Data Quality
- Higher Quality Content
- 60% Fewer Hallucinations
Browse by: Latest US Patents, China's latest patents, Technical Efficacy Thesaurus, Application Domain, Technology Topic, Popular Technical Reports.
© 2025 PatSnap. All rights reserved.Legal|Privacy policy|Modern Slavery Act Transparency Statement|Sitemap|About US| Contact US: help@patsnap.com