Anti-cracking and anti-permeability lightweight aggregate insulating concrete
A technology of thermal insulation concrete and lightweight aggregate, applied in the field of building materials, can solve the problems of insufficient thermal insulation performance of finished products, different quality of extruded plastic boards, low overall strength and wear resistance, etc. The effect of strengthening pumping and compressive strength and reducing construction costs
- Summary
- Abstract
- Description
- Claims
- Application Information
AI Technical Summary
Problems solved by technology
Method used
Examples
Embodiment 1
[0015] Example 1: This example describes the preparation and construction of an anti-seepage and anti-crack lightweight aggregate thermal insulation concrete.
[0016] The first part, the preparation of powder: add 600 kg of Portland cement, 300 kg of quartz sand, 50 kg of nano-silica fume, 40 kg of fly ash or slag powder, 100 kg of sepiolite, 28 Kg of waterproof dispersible latex powder, 4.2 kg of early strength agent (commercially available), 20 kg of osmotic crystallization active masterbatch, 12 kg of durafiber, 50 kg of powder acrylic milk cement modifier, add dry blender and mix Then made into dry powder.
[0017] In the second part, through the foaming machine, add 2kg of gelling liquid per cubic meter, inflate with water to make viscous foam, mix the dry powder and viscous foam evenly, and pump it to the construction site through pumping equipment, use an aluminum alloy ruler according to the design Construction requires smoothing.
Embodiment 2
[0018] Example 2: This example describes the preparation and construction of an anti-seepage and anti-crack lightweight aggregate thermal insulation concrete.
[0019] The first part, the preparation of powder: add 550 kg of Portland cement, 340 kg of quartz sand, 65 kg of nano silica fume, 50 kg of fly ash or slag powder, 100 kg of sepiolite, 27 Kg of waterproof dispersible latex powder, 3.85 kg of early strength agent (commercially available), 9 kg of osmotic crystallization active masterbatch, 10 kg of durafiber, 35 kg of powder acrylic milk cement modifier, add dry blender and mix Then made into dry powder.
[0020] In the second part, through the foaming machine, add 2kg of gelling liquid per cubic meter, inflate with water to make viscous foam, mix the dry powder and viscous foam evenly, and pump it to the construction site through pumping equipment, use an aluminum alloy ruler according to the design Construction requires smoothing.
Embodiment 3
[0021] Example 3: This example describes the preparation and construction of an anti-seepage and anti-crack lightweight aggregate thermal insulation concrete.
[0022] The first part, the preparation of powder: add 520 kg of Portland cement, 480 kg of quartz sand, 55 kg of nano silica fume, 80 kg of fly ash or slag powder, 100 kg of sepiolite, 25 kg Kg of waterproof dispersible latex powder, 3.64 kg of early strength agent (commercially available), 10 kg of osmotic crystallization active masterbatch, 9 kg of durafiber, 32 kg of powder acrylic milk cement modifier, add dry blender and mix Then made into dry powder.
[0023] In the second part, through the foaming machine, add 2kg of gelling liquid per cubic meter, inflate with water to make viscous foam, mix the dry powder and viscous foam evenly, and pump it to the construction site through pumping equipment, use an aluminum alloy ruler according to the design Construction requires smoothing.
PUM
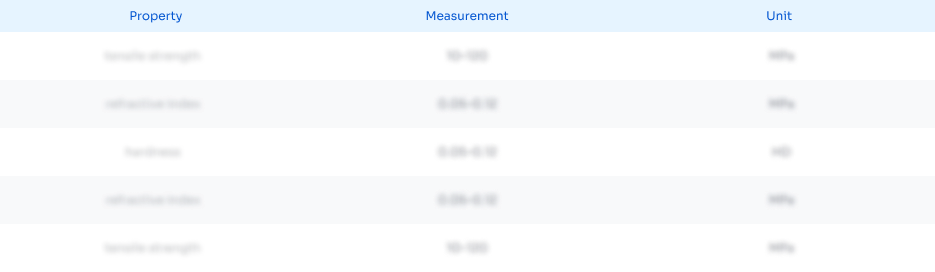
Abstract
Description
Claims
Application Information

- Generate Ideas
- Intellectual Property
- Life Sciences
- Materials
- Tech Scout
- Unparalleled Data Quality
- Higher Quality Content
- 60% Fewer Hallucinations
Browse by: Latest US Patents, China's latest patents, Technical Efficacy Thesaurus, Application Domain, Technology Topic, Popular Technical Reports.
© 2025 PatSnap. All rights reserved.Legal|Privacy policy|Modern Slavery Act Transparency Statement|Sitemap|About US| Contact US: help@patsnap.com